Introduction
Welding stands as a cornerstone of the Nigerian industry, playing a pivotal role in the fabrication and maintenance of essential infrastructure and equipment.
This process involves the fusion of materials, primarily metals, to create strong, durable joints critical for structural integrity and operational safety.
The Nigerian industry relies heavily on welding for diverse applications across sectors such as construction, manufacturing, oil and gas, and transportation.
In construction, welding ensures the stability and longevity of buildings, bridges, and roads, thereby supporting urban development and infrastructure expansion initiatives.
Moreover, welding practices in manufacturing contribute to the production of machinery, industrial equipment, and consumer goods essential for economic growth.
The oil and gas sector depends on welding for pipelines, offshore platforms, and refineries, where precision and reliability are paramount to prevent leaks and ensure operational efficiency.
In essence, welding not only facilitates the creation of robust structures but also plays a critical role in maintaining safety standards and operational reliability within Nigeria’s industrial landscape.
Types of Welding Processes
Various Welding Techniques Commonly Used in the Nigerian Industry
In the Nigerian industry, several welding techniques cater to diverse applications and material types. Metal Inert Gas (MIG) welding utilizes a continuous wire electrode and inert gas shield, ideal for high-speed welding of thicker materials in industries like manufacturing and automotive.
Tungsten Inert Gas (TIG) welding offers precise control over the welding arc, making it suitable for welding thin materials and exotic metals such as stainless steel and aluminum. This technique is favored in sectors requiring high-quality welds, such as aerospace and precision engineering.
Arc welding, including Shielded Metal Arc Welding (SMAW) and Gas Metal Arc Welding (GMAW), involves creating an electric arc between the base metal and a consumable electrode.
It is versatile and widely used across various sectors in Nigeria, including construction, shipbuilding, and general fabrication.
Gas welding, which includes Oxy-fuel welding and cutting, relies on a flame produced by burning a mixture of fuel gas and oxygen. This method is portable and suitable for welding pipes, small metal parts, and artistic metalwork.
Differences Between Techniques like MIG, TIG, Arc, and Gas Welding
The main differences among these techniques lie in their application, the type of materials they can weld effectively, and the specific characteristics of the weld they produce.
MIG welding excels in speed and productivity, making it ideal for thicker materials and high-volume production settings.
TIG welding, characterized by precise control and clean welds, is suited for thinner materials and applications where weld appearance and quality are paramount.
Arc welding techniques provide versatility across a range of materials and thicknesses, offering simplicity and effectiveness in various industrial applications.
Gas welding, with its portable nature and suitability for smaller-scale projects, remains relevant in sectors requiring flexibility and maneuverability.
Choosing the right welding technique depends on factors such as material thickness, project specifications, and desired weld characteristics.
Welders in Nigeria benefit from proficiency in multiple techniques, ensuring they can meet diverse industry demands and uphold standards of quality and reliability in welded structures and components.
In summary, the Nigerian industry leverages a spectrum of welding techniques to support infrastructure development, manufacturing processes, and technological advancements.
By understanding and mastering methods like MIG, TIG, Arc, and Gas welding, welders contribute to the nation’s industrial growth and maintain excellence in welding practices across various sectors.
Read: Career Opportunities in Agricultural Engineering in Nigeria
Safety Measures in Welding
Necessary Safety Precautions that Welders in Nigeria Should Take
Safety precautions are crucial for welders in Nigeria to mitigate the inherent risks associated with welding processes. These precautions are essential to protect both the welders themselves and those working nearby.
First and foremost, welders should wear appropriate personal protective equipment (PPE) at all times.
This includes welding helmets with proper eye protection, gloves, flame-resistant clothing, and steel-toed boots. These items shield against sparks, UV radiation, and potential burns during welding operations.
Proper ventilation is equally critical to minimize exposure to hazardous fumes and gases produced during welding. Adequate airflow in the workspace helps dissipate smoke and contaminants, maintaining air quality and reducing the risk of respiratory issues among workers.
Comprehensive training and education are fundamental aspects of welding safety. Welders should undergo thorough training on welding techniques, equipment operation, and safety protocols before commencing work.
This training not only enhances their skills but also increases awareness of potential hazards and the correct procedures to mitigate them. Ongoing training updates on new technologies and safety regulations further reinforce competence and readiness.
Regular maintenance and inspection of welding equipment are essential to ensure functionality and safety. Faulty or poorly maintained equipment not only increases the risk of accidents but also compromises the quality of welds.
Routine checks and timely repairs prevent potential hazards and ensure optimal performance of welding tools and machinery.
Importance of Protective Gear, Proper Ventilation, and Training to Prevent Accidents and Health Hazards
Protective gear such as welding helmets, gloves, flame-resistant clothing, and boots not only safeguard against immediate hazards like sparks and heat but also protect against long-term health risks from UV radiation and fumes.
Proper ventilation systems in welding areas are crucial to maintaining air quality and reducing respiratory risks associated with welding fumes, which can contain harmful substances such as chromium, nickel, and manganese.
Training and education ensure that welders understand the risks associated with their work and are equipped with the knowledge to use equipment safely and effectively.
This knowledge includes understanding safety procedures, recognizing hazards, and responding appropriately in emergencies.
Regular training updates keep welders informed about new safety regulations, technologies, and techniques, allowing them to continuously improve their skills and maintain high safety standards in the workplace.
By prioritizing safety measures such as the use of protective gear, ensuring proper ventilation, and providing comprehensive training, welders in Nigeria not only protect themselves from accidents and health hazards but also contribute to a safer and more productive work environment overall.
These practices are essential for upholding standards of excellence in the welding industry and promoting the well-being of all workers involved in welding operations.
Read: Admission Requirements for Agricultural Engineering Programs
Quality Control in Welding
Significance of Quality Control in Welding to Meet Industry Standards
Quality control in welding is fundamental to ensuring that welded structures and components meet stringent industry standards. It encompasses a systematic approach to verify weld integrity, reliability, and adherence to specified requirements.
In the Nigerian industry, where welding plays a crucial role in construction, manufacturing, and oil and gas sectors, maintaining high-quality welds is essential.
Welded components must withstand operational stresses, environmental conditions, and safety requirements, making quality control a cornerstone of project success and longevity.
Adhering to industry standards through rigorous quality control processes ensures that welded joints perform as intended, minimizing the risk of structural failures or operational disruptions.
This is particularly critical in sectors such as infrastructure development, where the safety and durability of welded connections directly impact public safety and project sustainability.
Techniques like Non-Destructive Testing (NDT) and Inspection Procedures to Ensure Welding Quality
Non-destructive testing (NDT) techniques are pivotal in verifying weld quality without compromising the integrity of the welded joint. These techniques include
- Ultrasonic Testing (UT): Utilizes high-frequency sound waves to penetrate welds and detect internal defects such as cracks, inclusions, or incomplete fusion. UT provides detailed insights into weld integrity and is particularly effective for thicker materials.
- Radiographic Testing (RT): Involves the use of X-rays or gamma rays to create images of the weld cross-section. RT reveals internal discontinuities like porosity, lack of fusion, or foreign materials, ensuring weld strength and reliability.
- Magnetic Particle Testing (MT): Applies magnetic fields and iron particles to the weld surface to detect surface and near-surface flaws. MT is effective for ferromagnetic materials and detects defects that may compromise weld integrity.
- Dye Penetrant Testing (PT): Uses capillary action to draw a fluorescent or colored dye into surface-breaking defects. After excess dye is removed, a developer is applied to highlight indications of flaws, ensuring thorough surface inspection.
Visual inspection remains integral, where qualified inspectors visually examine welds for surface imperfections, weld bead profiles, and adherence to welding specifications.
Documenting inspection results and maintaining comprehensive records are crucial for traceability and quality assurance. This documentation ensures that welds meet regulatory requirements and project specifications, facilitating certification and client approval.
Continuous improvement in welding practices, guided by feedback from inspection findings, enhances process efficiency and weld quality.
Implementing corrective actions based on NDT results and inspection reports reinforces welding procedures, mitigates risks, and ensures consistency in weld performance.
Read: Impact of Agricultural Engineering on Crop Production
Best Practices for Welding Efficiency
Best practices to enhance welding productivity in the Nigerian industry
In Nigeria’s diverse industrial sector, optimizing welding processes is essential for maintaining competitiveness and ensuring high-quality outputs. Here are comprehensive tips to enhance welding productivity:
Proper Material Preparation
Effective welding begins with meticulous material preparation. Start by thoroughly cleaning all surfaces to remove rust, dirt, oils, and other contaminants.
This step is crucial as it ensures a clean base for welding, minimizing the risk of defects and ensuring strong, durable welds.
Inspect materials for any imperfections or inconsistencies that could affect weld quality and integrity. Selecting the correct filler materials and storing them properly maintains their integrity during handling.
Correct Welding Positioning
The positioning of materials during welding plays a significant role in achieving optimal results. Ensure that workpieces are securely positioned and aligned according to welding specifications.
Use fixtures, jigs, and supports to maintain alignment and stability throughout the welding process.
Proper positioning not only enhances weld quality by reducing distortion and improving accessibility but also minimizes operator fatigue. This practice contributes to increased efficiency and consistency in production.
Effective Equipment Maintenance
Regular maintenance and upkeep of welding equipment are essential for achieving consistent performance and minimizing downtime.
Develop a scheduled maintenance routine that includes cleaning, inspection, lubrication, and calibration of welding machines, torches, and accessories.
Replace worn-out parts promptly to prevent equipment failure during critical welding operations. Properly maintained equipment operates more efficiently, delivers more consistent welds, and extends the lifespan of valuable welding assets.
Use of Appropriate Welding Techniques
Selecting the right welding technique is paramount to achieving optimal results in different welding applications.
Evaluate factors such as material type, thickness, joint configuration, and production requirements to determine whether MIG (Metal Inert Gas), TIG (Tungsten Inert Gas), stick welding, or other specialized techniques are most suitable.
Each technique offers unique advantages in terms of weld quality, speed, and versatility. Implementing the appropriate technique ensures efficient use of resources and enhances overall productivity.
Continuous Skills Development
Investing in the skills and proficiency of welding operators is crucial for maintaining high standards of productivity and safety.
Provide ongoing training programs that cover welding techniques, safety protocols, equipment operation, and industry best practices. Encourage operators to stay updated on technological advancements and emerging trends in welding technology.
Continuous skills development not only enhances individual performance but also fosters a culture of continuous improvement within the workforce.
Implementing these best practices fosters welding efficiency in the Nigerian industry.
Thorough material preparation, precise welding positioning, proactive equipment maintenance, appropriate techniques, and continuous skills development boost productivity, quality, and safety in businesses.
These strategies not only optimize operational processes but also contribute to sustainable growth and competitiveness in the global market.
Read: Challenges Facing Agricultural Engineers in Nigeria
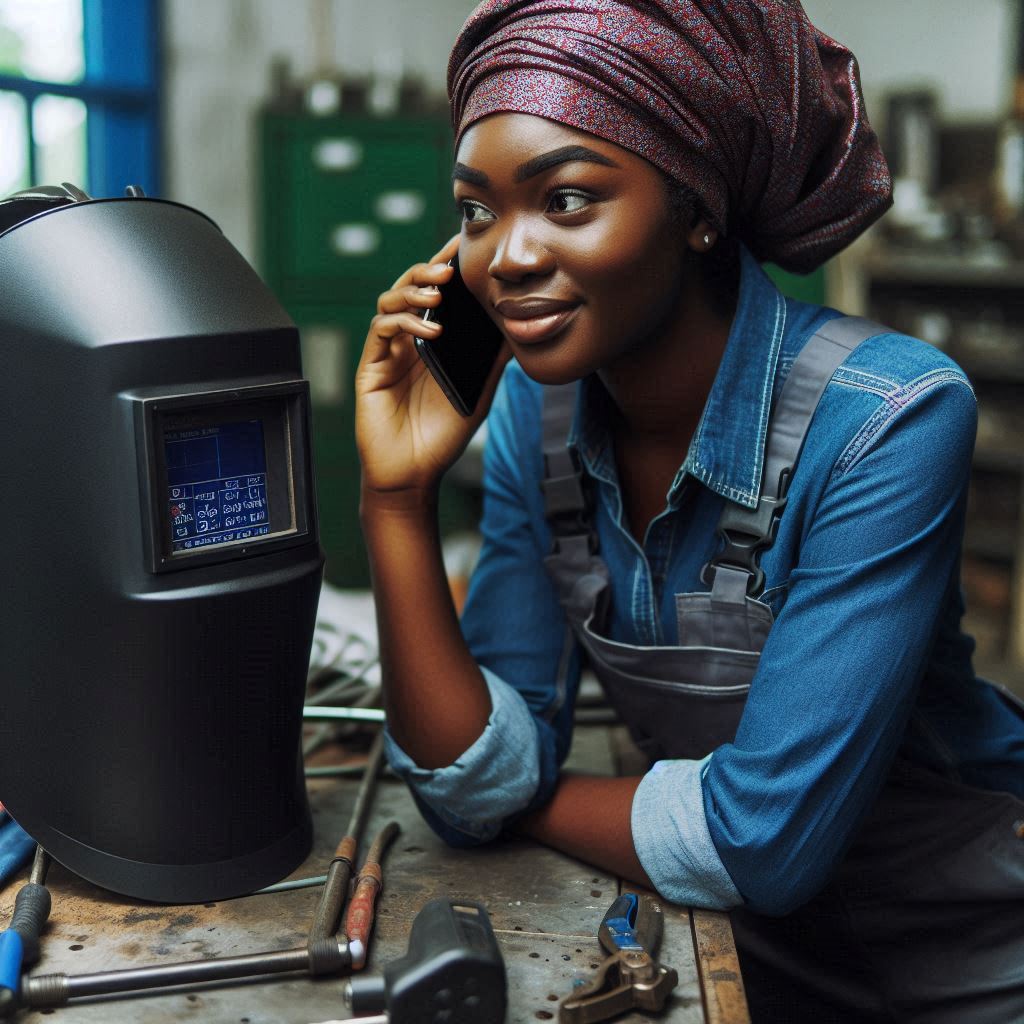
Environmental Impact of Welding
Environmental Concerns Associated with Welding Activities in Nigeria
Welding activities in Nigeria pose significant environmental challenges that require attention and proactive management.
Air pollution is a major concern due to welding fumes and gases containing harmful substances like particulate matter, ozone, nitrogen oxides, and volatile organic compounds (VOCs).
These emissions not only degrade air quality but also pose health risks to workers and nearby communities.
Transform Your Career with Expert Guidance
Get personalized mentorship consulting that’s tailored to your unique path. Our expert advice is actionable and exclusive.
Get StartedWelding operations produce noise pollution that impacts both workers’ health and the surrounding environment, requiring noise control measures.
Ways to Reduce Pollution and Waste Generation During Welding Operations for a Sustainable Industry
To promote environmental sustainability in the welding industry, several strategies can be implemented:
Improved Ventilation Systems
Install effective local exhaust ventilation (LEV) systems to capture welding fumes and gases at the source, preventing their release into the atmosphere. Proper ventilation reduces exposure risks and improves indoor air quality.
Use of Low-Emission Processes
Encourage the adoption of welding processes with lower emissions, such as gas metal arc welding (GMAW) instead of shielded metal arc welding (SMAW). GMAW generates fewer fumes and requires less post-weld cleaning, contributing to cleaner air and reduced environmental impact.
Substitution of Cleaner Materials
Where feasible, substitute welding materials and consumables with lower emissions and environmental impact. Choose low-emission coatings, gases, and filler metals to minimize pollution during welding operations.
Proper Waste Management
Implement effective waste management practices to handle welding residues, spent consumables, and hazardous materials responsibly. Recycling and proper disposal reduce landfill contributions and prevent environmental contamination.
Training and Awareness
Educate welders and industry professionals about environmental impacts and best practices for pollution prevention and waste reduction. Training programs on sustainable welding techniques empower workers to make environmentally conscious decisions.
Monitoring and Compliance
Regularly monitor emissions and ensure compliance with environmental regulations to identify areas needing improvement and maintain standards. Monitoring helps track progress in pollution reduction and ensures accountability within the industry.
By addressing environmental concerns and adopting sustainable practices, the Nigerian welding industry can reduce its environmental footprint and support public health goals.
Promoting cleaner technologies, improving ventilation, managing waste responsibly, and raising environmental awareness are vital for sustainability in Nigeria’s welding sector.
In essence, proactive measures to reduce pollution and manage waste effectively not only protect the environment and public health but also enhance the sustainability and reputation of Nigeria’s welding industry.
Embracing sustainable practices ensures a greener future while supporting economic growth and industry development.
Conclusion
It is imperative for the welding industry in Nigeria to adopt and implement the best practices discussed in this blog post.
Adhering to these practices will not only ensure the quality of the welds but also guarantee the safety of the operators and the environment.
Consistently training and certifying welders, maintaining equipment properly, and using appropriate PPE are crucial for successful welding operations.
By following best welding practices, Nigerian industries can enhance efficiency, productivity, and overall operational success.
It is essential for all stakeholders in the welding sector to recognize the significance of compliance with these best practices to achieve sustainable growth in the industry.
Therefore, a collective effort is needed to promote a culture of safety, quality, and professionalism in welding practices across Nigeria.
Ultimately, prioritizing best welding practices will not only elevate the standards of the industry but also contribute to a safer and more sustainable working environment for all involved.