Introduction
The Nigerian welding industry is a cornerstone of various economic sectors, vital for infrastructure development, manufacturing, and construction. It underpins the creation of critical structures like bridges, pipelines, and industrial machinery.
Despite its significance, the industry grapples with formidable challenges. Inadequate training and certification standards pose barriers to skilled labor development.
Furthermore, the sector contends with inconsistent power supply, which disrupts operations and affects productivity. Access to modern welding equipment and technologies remains limited, hindering efficiency and innovation.
Nevertheless, welding remains indispensable for Nigeria’s economic growth and development. Addressing these challenges is crucial to enhance productivity, ensure safety standards, and bolster the industry’s global competitiveness.
Stakeholders must collaborate to implement strategic interventions that promote skill enhancement, technology adoption, and infrastructure improvement.
As we explore the complexities of the Nigerian welding landscape, it becomes evident that proactive measures and investments are essential.
By acknowledging both the importance and challenges of welding, stakeholders can pave the way for a resilient and thriving industry poised for sustainable advancement.
Lack of skilled workforce
Shortage of trained welders in Nigeria
The Nigerian welding industry faces a critical shortage of trained welders, impacting various sectors. This scarcity stems from inadequate vocational training programs and a lack of emphasis on skilled trades.
As demand for welding expertise grows across construction, manufacturing, and oil and gas sectors, the shortage exacerbates.
Impact on the quality of welding projects
The shortage of trained welders directly affects the quality and efficiency of welding projects. Inexperienced practitioners may compromise structural integrity and safety standards, leading to costly rework and project delays.
This issue not only undermines project timelines but also jeopardizes the overall safety and reliability of infrastructural developments.
Need for specialized training programs
Addressing the shortage necessitates the establishment of specialized training programs tailored to the needs of the Nigerian welding industry. These programs should emphasize hands-on skills development, safety protocols, and the use of advanced welding technologies.
By investing in comprehensive training initiatives, stakeholders can cultivate a competent workforce capable of meeting industry demands.
In response to these challenges, collaborative efforts between educational institutions, government agencies, and industry stakeholders are crucial. Vocational schools and technical colleges play a pivotal role in bridging the skills gap by offering accredited welding courses.
These programs should integrate practical apprenticeships and internships to provide real-world experience and ensure graduates are job-ready.
Furthermore, industry leaders must advocate for standardized certification processes to validate welders’ skills and competencies. Certifications not only enhance employability but also instill confidence in clients regarding the quality of workmanship.
To improve the quality of welding projects, investment in modern welding equipment and technologies is imperative. Access to state-of-the-art machinery enhances precision, efficiency, and overall project outcomes.
Additionally, initiatives promoting continuous professional development among practicing welders contribute to skill enhancement and adaptation to evolving industry standards.
Therefore, addressing the shortage of trained welders in Nigeria requires a concerted effort to overhaul vocational training programs and promote specialized education.
By prioritizing skills development and investing in infrastructure and certification, stakeholders can elevate the standards of the Nigerian welding industry.
This proactive approach not only strengthens the workforce but also ensures sustainable growth and competitiveness in the global market.
Read: Top Universities for Agricultural Engineering in Nigeria
Inadequate infrastructure
Limited access to modern welding equipment and technology
The Nigerian welding industry faces significant challenges due to limited access to modern equipment and technology.
Many welding firms operate with outdated machinery, which hampers their ability to compete effectively in the global market.
Modern welding equipment is crucial for achieving precision, efficiency, and high-quality welds, essential for meeting stringent industry standards.
Challenges faced due to poor infrastructure
Poor infrastructure exacerbates challenges in the Nigerian welding sector. Inconsistent power supply disrupts operations, leading to downtime and increased costs.
Additionally, inadequate transportation networks and logistical inefficiencies hinder the timely delivery of materials and equipment to project sites. These infrastructure shortcomings contribute to project delays, compromising overall productivity and client satisfaction.
Importance of updating infrastructure for the growth of the industry
Updating infrastructure is paramount for driving growth and competitiveness in the Nigerian welding industry. Improved access to reliable electricity would enhance operational reliability and reduce downtime.
Upgraded transportation networks would facilitate the efficient movement of goods and equipment, minimizing delays and optimizing project timelines.
Investing in modern welding technologies not only boosts productivity but also ensures that Nigerian welders can meet global quality standards and compete effectively in international markets.
Addressing these challenges requires a multi-faceted approach involving collaboration between government agencies, private sector stakeholders, and educational institutions.
Government policies should prioritize infrastructure development, with targeted investments in power generation, transportation networks, and technological innovation.
Incentives for private sector involvement in infrastructure projects can stimulate investment and foster technological advancements within the welding industry.
Furthermore, vocational training programs must evolve to incorporate training on modern welding technologies and practices.
Hands-on workshops and apprenticeships should be integrated into curricula to ensure that welders are proficient in using advanced equipment.
Certification programs should align with international standards to enhance the employability and global competitiveness of Nigerian welders.
Most Importantly, addressing the challenges of limited access to modern equipment, poor infrastructure, and the need for technological advancement is essential for the growth and sustainability of the Nigerian welding industry.
By investing in infrastructure development, promoting technological innovation, and enhancing vocational training, Nigeria can strengthen its position as a leader in the global welding market while driving economic growth and development.
Read: Entrepreneurial Opportunities in Agricultural Engineering
Safety Concerns
Lack of adherence to safety standards in welding practices
The Nigerian welding industry grapples with a lack of adherence to safety standards, posing significant risks to workers and projects. Many firms overlook proper safety protocols due to inadequate training and oversight.
High rate of welding-related accidents and injuries
As a consequence of lax safety practices, the Nigerian welding sector experiences a high rate of accidents and injuries. These incidents not only endanger workers’ lives but also lead to project delays, increased costs, and reputational damage for companies involved.
Importance of promoting safety measures in the industry
Promoting stringent safety measures is imperative for the Nigerian welding industry’s growth and sustainability.
Implementing comprehensive safety training programs, enforcing adherence to safety regulations, and investing in appropriate safety equipment are critical steps.
By prioritizing safety, companies can create safer work environments, enhance worker morale and productivity, and mitigate financial and legal risks associated with accidents.
To address these challenges effectively, collaboration among government agencies, industry associations, and educational institutions is essential.
Government bodies should enforce existing safety regulations and introduce new measures where necessary.
Industry leaders must prioritize safety as a core value and invest in ongoing training and certification programs for welders. Educational institutions should integrate safety practices into welding curricula to ensure that future welders are well-prepared to uphold safety standards in their careers.
Furthermore, fostering a culture of safety requires ongoing awareness campaigns and initiatives to educate stakeholders about the importance of safety in welding operations.
Companies should incentivize and reward adherence to safety protocols to create a culture where safety is non-negotiable.
Basically, addressing the challenges of safety standards in Nigerian welding practices requires a concerted effort from all stakeholders.
By promoting and enforcing strict safety measures, Nigeria can enhance the reputation and competitiveness of its welding industry while safeguarding the well-being of its workforce.
Read: Career Opportunities in Agricultural Engineering in Nigeria
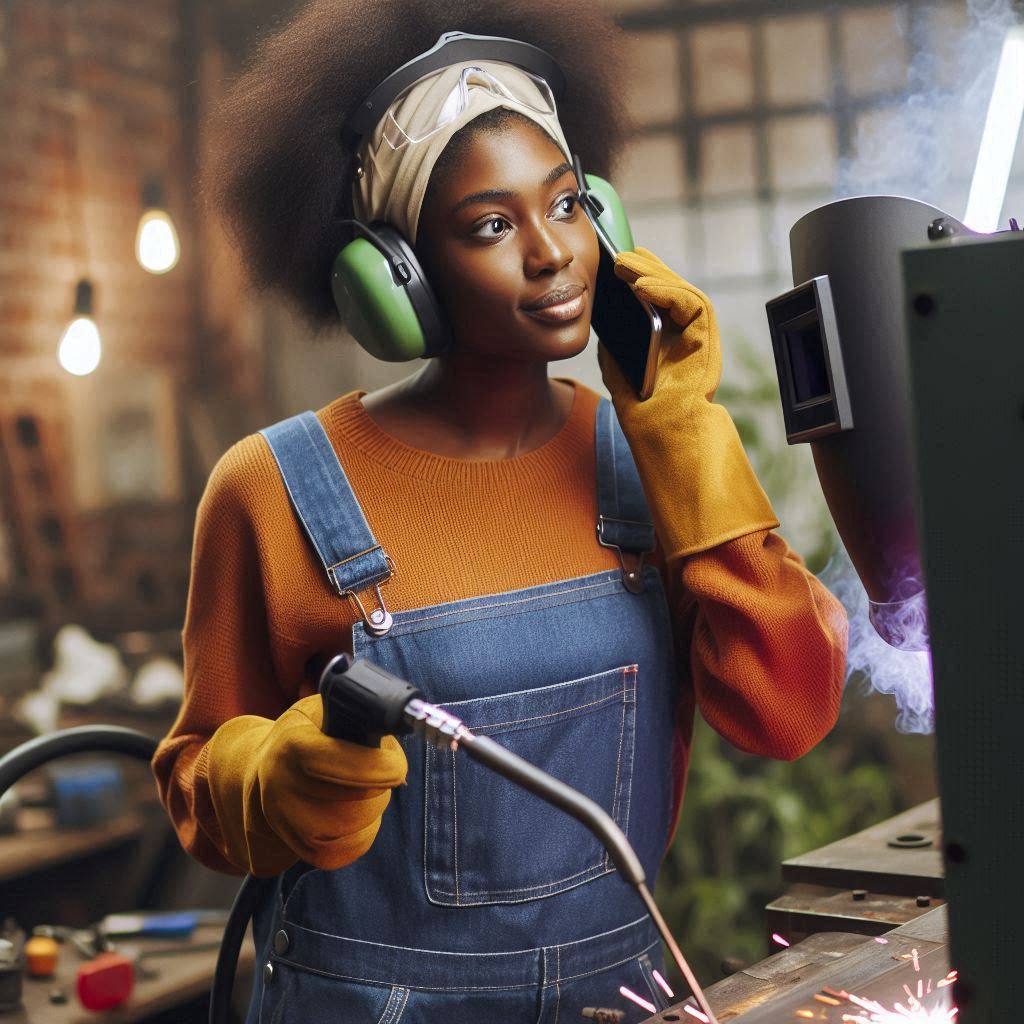
Discover More: Open Source Contributions by Nigerian Engineers
See Related Content: Mobile Network Operators in Nigeria
Inconsistent Regulations and Standards
Inconsistent regulations and standards in the welding industry
The Nigerian welding industry faces significant challenges stemming from inconsistent regulations and standards. Across different regions and sectors, varying regulatory frameworks create confusion and compliance difficulties for businesses and practitioners alike.
This inconsistency hampers the industry’s ability to operate efficiently and competently.
Challenges faced by welders due to regulatory gaps
Welders encounter numerous challenges due to regulatory gaps in Nigeria’s welding industry. These gaps manifest in unclear guidelines regarding safety protocols, certification requirements, and environmental standards.
As a result, welders and welding companies struggle with operational inefficiencies, legal uncertainties, and the risk of non-compliance penalties.
The lack of standardized regulations also complicates cross-regional and international business engagements, limiting opportunities for growth and innovation.
Importance of streamlining regulations for effective operations
Streamlining regulations is paramount to fostering the effective operation and sustainable growth of Nigeria’s welding industry. Clear, standardized regulations would enhance compliance, streamline operations, and create a level playing field for businesses.
By establishing uniform standards and consistent enforcement mechanisms, stakeholders can mitigate compliance risks, improve safety practices, and bolster the industry’s reputation for quality and reliability.
To address these regulatory challenges comprehensively, collaborative efforts among government entities, industry associations, legal experts, and educational institutions are essential.
Government agencies should undertake rigorous assessments of existing regulations, identifying inconsistencies, gaps, and opportunities for improvement.
Through stakeholder consultations and regulatory updates, policymakers can develop robust frameworks that align with international best practices while addressing local needs and priorities.
Industry stakeholders must actively engage in regulatory discussions, advocating for practical and enforceable standards that promote safety, innovation, and sustainable development.
Training and capacity-building programs should integrate updated regulatory requirements to ensure that welders and industry professionals are well-prepared and compliant with evolving standards.
Moreover, promoting transparency and accountability in regulatory processes is crucial for building trust and confidence within the industry. Regular reviews and assessments of regulatory impacts can facilitate continuous improvement and adaptation to changing market dynamics.
Essentially, overcoming the challenges posed by inconsistent regulations in the Nigerian welding industry requires a concerted effort to streamline and harmonize regulatory frameworks.
By prioritizing regulatory clarity, Nigeria can enhance business certainty, stimulate investment, and strengthen its position in the global welding market. This strategic approach will not only support industry growth but also contribute to national economic development and job creation in the long term.
Read: Admission Requirements for Agricultural Engineering Programs
Discover More: Essential Skills for Nigerian Software Engineers
Economic challenges
In the Nigerian welding industry, economic challenges play a significant role in hindering the growth and development of the sector.
These challenges can range from the high cost of importing welding equipment and materials, to the impact of fluctuating exchange rates on the industry. Additionally, there is a growing importance of developing local capacity for sustainability in the industry.
High cost of importing welding equipment and materials
One of the major economic challenges facing the Nigerian welding industry is the high cost of importing welding equipment and materials. This cost can be attributed to various factors such as import duties, transportation costs, and foreign exchange rates.
These high costs make it difficult for local welders and welding companies to acquire the necessary equipment and materials to carry out their work effectively.
Impact of fluctuating exchange rates on the industry
Another economic challenge facing the Nigerian welding industry is the impact of fluctuating exchange rates on the sector. The industry heavily relies on imported equipment and materials, which are purchased using foreign currency.
Fluctuations in exchange rates can significantly affect the cost of importing these materials, leading to increased expenses for welding companies. This can ultimately result in higher prices for customers, making welding services less competitive in the market.
Importance of developing local capacity for sustainability
To address the economic challenges facing the Nigerian welding industry, there is a growing importance of developing local capacity for sustainability. This involves investing in local manufacturing capabilities to produce welding equipment and materials locally.
By reducing reliance on imports, the industry can mitigate the impact of fluctuating exchange rates and high import costs. Developing local capacity also creates job opportunities and stimulates economic growth within the country.
Generally, economic challenges pose significant obstacles to the growth and sustainability of the Nigerian welding industry.
By addressing issues such as the high cost of importing equipment and materials, managing fluctuating exchange rates, and investing in local capacity, the industry can overcome these challenges and thrive in the long run.
Gain More Insights: Comparing Nigerian and International Civil Engineering Practices
Transform Your Career with Expert Guidance
Get personalized mentorship consulting that’s tailored to your unique path. Our expert advice is actionable and exclusive.
Get StartedFind Out More: Chemical Engineering Innovations from Nigeria
Conclusion
The Nigerian welding industry confronts formidable challenges that hinder its progress and competitiveness. A shortage of trained welders, coupled with limited access to modern equipment and technology, impedes operational efficiency and quality.
Inconsistent regulations further complicate matters, leading to compliance issues and safety concerns. Stakeholders across government, industry, and education sectors must collaborate urgently.
They should prioritize the development of robust training programs to address the skills gap and ensure a steady supply of qualified welders.
Investment in infrastructure upgrades, including reliable power supply and advanced welding technologies, is crucial for enhancing productivity and meeting global standards.
Streamlining regulations to create a unified framework will promote clarity and compliance, fostering a safer and more conducive business environment.
These collective efforts are essential to unlock the industry’s potential for growth and development. By overcoming these challenges together, Nigeria can fortify its welding sector, stimulate economic growth, and elevate its position in the global marketplace.