Introduction
Quantity surveying involves managing and controlling costs within construction projects. lets discuss on quantity surveying cost control techniques.
Quantity surveyors play a critical role in ensuring projects remain financially viable and are completed within budget.
They handle cost estimation, budgeting, procurement, and financial reporting, among other responsibilities. Effective cost control techniques are essential to ensure that projects do not exceed their financial limits and are executed efficiently.
Cost control techniques are vital in the construction industry for several reasons. First, they help minimize wastage and ensure resources are used optimally.
By monitoring and controlling costs, quantity surveyors can prevent unnecessary expenses and identify areas where savings can be made.
Second, these techniques enhance project efficiency and productivity. By keeping track of costs and implementing cost-saving measures, quantity surveyors contribute to the timely completion of projects.
Third, effective cost control techniques ensure profitability. By managing costs effectively, quantity surveyors help maximize returns on investment for stakeholders.
This blog post will explore various cost control techniques employed by quantity surveyors. We will discuss how these techniques are implemented throughout the project lifecycle, from initial cost estimation to final financial reporting.
Understanding these methods is crucial for maintaining budgetary discipline and delivering successful construction projects.
Through detailed analysis and practical examples, we aim to provide insights into the strategies that quantity surveyors use to control costs and ensure financial success in construction projects.
Cost Estimation in Quantity Surveying
Cost estimation is a fundamental aspect of quantity surveying. It involves predicting the financial resources needed to complete a construction project accurately.
Accurate cost estimation ensures projects are financially viable and helps prevent budget overruns. In this blog post, we will discuss the process of estimating costs, explore different methods of cost estimation, and highlight the importance of accuracy in cost estimation.
Process of Estimating Costs in Quantity Surveying
The process of cost estimation in quantity surveying starts with understanding the project scope. Quantity surveyors review architectural plans, specifications, and client requirements.
They identify all components and activities required to complete the project. This comprehensive understanding forms the basis for accurate cost estimation.
Next, quantity surveyors collect and analyze data on material prices, labor rates, equipment costs, and other expenses.
They use historical data, market research, and supplier quotes to gather this information. This data collection is crucial for developing realistic cost estimates.
Quantity surveyors then prepare detailed cost breakdowns for each project component. They estimate the costs of materials, labor, equipment, subcontractor fees, and overheads.
This detailed analysis helps in creating a comprehensive cost estimate. It is essential to consider factors such as inflation, market volatility, and potential project changes that could impact costs.
The final step in the cost estimation process is compiling the data into a formal report.
This report provides a clear and concise presentation of the estimated costs, including a summary of assumptions, methodologies, and any contingencies considered. The report is then reviewed with stakeholders to ensure alignment and approval before moving forward.
Different Methods of Cost Estimation
Several methods of cost estimation are used in quantity surveying. Each method has its advantages and is suitable for different project stages and types.
The first method is the Preliminary Estimate. This method provides an approximate cost estimate based on limited project information.
It is useful in the early stages of project planning when detailed designs are not yet available. Preliminary estimates help stakeholders make informed decisions about project feasibility and scope.
The second method is the Detailed Estimate. This method involves a comprehensive analysis of all project components and activities.
Quantity surveyors use detailed plans, specifications, and accurate data to develop this estimate. It is more precise and suitable for the final budgeting and tendering phases. Detailed estimates are crucial for securing financing and setting realistic project budgets.
Another method is the Unit Rate Estimation. Quantity surveyors calculate costs based on standard unit rates for materials and labor. They multiply these rates by the quantities required for the project.
This method is useful for projects with repetitive activities and standard specifications. Unit rate estimation allows for quick and consistent cost calculations across similar projects.
The Cost Plan method involves breaking down the project into stages and estimating costs for each stage.
This approach helps in monitoring costs throughout the project lifecycle and ensures that budgets are adhered to at each stage. Cost plans are dynamic documents that can be adjusted as the project progresses and new information becomes available.
Importance of Accurate Cost Estimation
Accurate cost estimation is critical for several reasons. First, it ensures that projects are financially feasible and helps secure funding from investors and financial institutions.
Accurate estimates provide confidence that the project can be completed within budget, making it easier to obtain the necessary financial backing.
Second, accurate cost estimation helps prevent budget overruns and financial surprises. By predicting costs accurately, quantity surveyors can identify potential cost overruns early and implement corrective measures.
This proactive approach minimizes the risk of financial strain and ensures that projects remain on track.
Third, accurate cost estimation enhances project planning and scheduling. It allows for efficient resource allocation and helps in setting realistic timelines and milestones.
Accurate estimates ensure that all project phases are adequately funded and resourced, reducing the likelihood of delays and disruptions.
Moreover, accurate cost estimation builds trust and credibility with clients, contractors, and stakeholders. It demonstrates a high level of professionalism and expertise, fostering positive relationships and collaboration.
Clients and stakeholders are more likely to engage in future projects with quantity surveyors who consistently deliver accurate and reliable cost estimates.
Read: Key Telecom Engineering Companies in Nigeria
Budgeting in Quantity Surveying
Budgeting plays a crucial role in quantity surveying. Effective budgeting ensures projects remain financially viable and meet client expectations.
Significance of Budgeting in Quantity Surveying
Budgeting is essential in quantity surveying for several reasons. It establishes a financial framework for the project, ensuring all expenses are accounted for. This financial planning helps avoid cost overruns and ensures resources are allocated efficiently.
A well-prepared budget also enhances decision-making. It provides a clear financial roadmap, guiding project managers in making informed choices. By anticipating costs and potential financial challenges, quantity surveyors can proactively address issues.
Moreover, budgeting builds client confidence. Clients feel reassured when they see a detailed and realistic budget, enhancing trust and satisfaction. It demonstrates professionalism and meticulous planning, key traits in successful project management.
Creating a Budget for Construction Projects
Creating a budget for construction projects involves several key steps. Start by thoroughly understanding the project’s scope and objectives. This foundational knowledge is crucial for accurate financial planning.
Next, conduct a detailed cost estimation. Break down the project into smaller tasks and estimate the costs associated with each. Include material costs, labor, equipment, and any other relevant expenses. Use historical data and industry benchmarks to enhance accuracy.
Engage with stakeholders early. Consult with contractors, suppliers, and other professionals to gather accurate cost information. Their input provides valuable insights and helps refine the budget.
Incorporate contingencies. Unexpected expenses can arise in any project. Allocate a contingency fund to cover unforeseen costs, ensuring the project remains financially stable.
Review and refine the budget regularly. As the project progresses, update the budget to reflect actual costs and any changes in scope. This ongoing review helps maintain financial control.
Tips for Effective Budget Management
Effective budget management requires continuous monitoring and proactive strategies. Here are some tips to ensure successful budget management in quantity surveying
- Track expenses meticulously: Keep detailed records of all expenditures. Regularly compare actual costs with budgeted amounts to identify variances early.
- Use project management software: Leverage technology to streamline budget tracking and reporting. Software tools provide real-time data and enhance accuracy.
- Communicate with the team: Ensure all team members are aware of the budget and its constraints. Foster a culture of financial responsibility.
- Negotiate with suppliers: Secure favorable terms and prices from suppliers. Negotiation skills can lead to significant cost savings.
- Review contracts carefully: Ensure all contracts are clear and comprehensive. Avoid vague terms that could lead to unexpected expenses.
- Implement cost-saving measures: Identify opportunities for cost savings without compromising quality. Efficient resource use and innovative techniques can reduce expenses.
- Regularly update stakeholders: Keep clients and other stakeholders informed about the budget status. Transparency builds trust and facilitates prompt issue resolution.
Basically, budgeting is a fundamental aspect of quantity surveying. Effective budgeting ensures projects remain financially viable, meet client expectations, and achieve successful outcomes.
By following these steps and tips, quantity surveyors can create and manage budgets efficiently, ensuring the financial success of construction projects.
Read: Government Support for Polymer Engineering in Nigeria
Value Engineering in Quantity Surveying
Value Engineering and Its Role in Cost Control
Firstly Value engineering is a systematic method used to improve the value of a project by optimizing its function and reducing costs. It plays a crucial role in cost control within quantity surveying.
By focusing on maximizing value while minimizing costs, quantity surveyors ensure projects are efficient and cost-effective.
Value engineering involves analyzing project functions to find ways to reduce costs without compromising quality or performance. Quantity surveyors use this approach to identify cost-saving opportunities throughout the project lifecycle.
This method ensures that the project delivers maximum value to stakeholders. Value engineering is integral to cost control, helping to achieve budget objectives and enhance project profitability.
Techniques for Maximizing Value While Minimizing Costs
Quantity surveyors employ various techniques to maximize value while minimizing costs.
One key technique is functional analysis. This involves breaking down the project into its essential functions and exploring alternative ways to achieve them more efficiently.
By rethinking design elements and construction methods, quantity surveyors can identify cost-saving opportunities.
Another technique is material substitution. Quantity surveyors evaluate different materials to find cost-effective alternatives that still meet project requirements. This process involves assessing durability, availability, and cost to ensure the chosen materials provide the best value.
Process optimization is another valuable technique. Quantity surveyors examine construction processes to identify inefficiencies and streamline operations. By improving workflows and reducing waste, they can significantly lower project costs.
Lifecycle costing is a comprehensive approach that considers the total cost of ownership, including initial costs, maintenance, and operational expenses. Quantity surveyors use this technique to select options that offer long-term value, balancing upfront savings with future costs.
Collaborative workshops are also effective in value engineering. Quantity surveyors work with architects, engineers, and contractors to brainstorm and evaluate cost-saving ideas. These collaborative efforts often result in innovative solutions that improve value and reduce costs.
Benefits of Implementing Value Engineering in Quantity Surveying
Implementing value engineering in quantity surveying offers numerous benefits. First, it enhances project efficiency by identifying and eliminating unnecessary costs. This proactive approach ensures projects stay within budget and deliver optimal value.
Second, value engineering improves project quality. By focusing on function and performance, quantity surveyors ensure that cost-saving measures do not compromise the project’s overall quality.
This balance between cost and quality leads to more successful project outcomes.
Third, value engineering fosters innovation. By challenging traditional methods and exploring alternative solutions, quantity surveyors encourage creativity and innovation in project design and execution.
This can lead to new and improved construction techniques and materials.
Fourth, value engineering enhances stakeholder satisfaction. By delivering projects that offer maximum value at reduced costs, quantity surveyors build trust and credibility with clients and stakeholders.
Satisfied stakeholders are more likely to engage in future projects and recommend the quantity surveyor’s services.
In fact, value engineering is a vital cost control technique in quantity surveying. By systematically analyzing project functions and exploring cost-saving opportunities, quantity surveyors can maximize value and minimize costs.
Implementing value engineering techniques leads to more efficient, high-quality, and innovative projects, ultimately benefiting all stakeholders involved.
Transform Your Career with Expert Guidance
Get personalized mentorship consulting that’s tailored to your unique path. Our expert advice is actionable and exclusive.
Get StartedRead: Nigerian Telecommunication Regulatory Bodies Explained
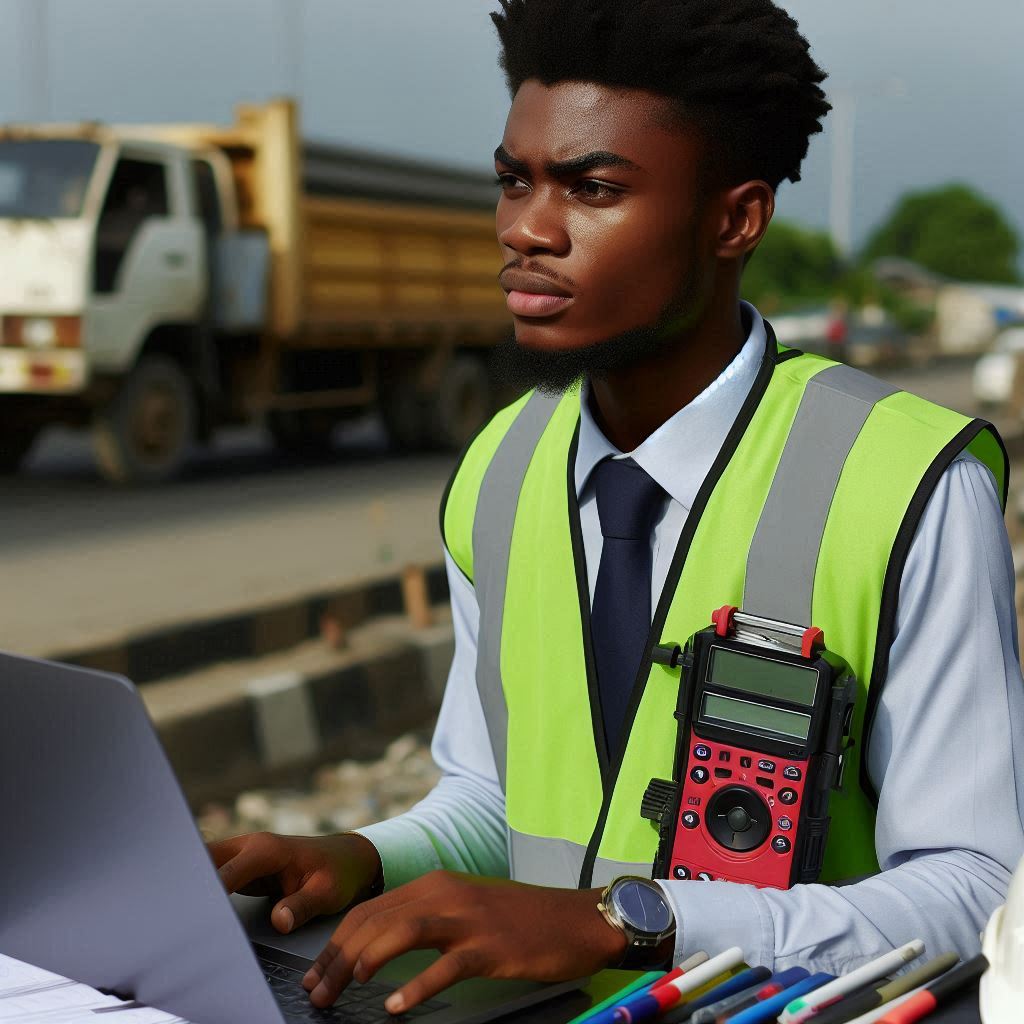
Risk Management in Quantity Surveying
Risk management is crucial in quantity surveying to control costs and ensure project success. Construction projects face various risks that can impact budgets and timelines.
Identify Common Risks in Construction Projects
Construction projects encounter multiple risks that can affect their progress and budget. Common risks include
- Cost Overruns: Unexpected expenses can push the project over budget, straining financial resources.
- Schedule Delays: Delays in project timelines can result from weather, supply chain disruptions, or labor shortages.
- Design Changes: Alterations to the project design can lead to additional costs and delays.
- Quality Issues: Poor workmanship or substandard materials can compromise the project’s integrity and necessitate costly repairs.
- Regulatory Compliance: Failing to meet legal and regulatory requirements can result in fines and project halts.
- Health and Safety: Accidents or health issues on-site can lead to delays and increased costs.
- Market Fluctuations: Changes in material prices or economic conditions can impact the project’s financial viability.
Strategies for Mitigating Risks and Controlling Costs
Implementing effective risk management strategies helps mitigate risks and control costs. Here are key strategies
- Conduct Thorough Risk Assessments: Identify potential risks early in the project. Analyze their likelihood and impact to prioritize mitigation efforts.
- Create Contingency Plans: Allocate contingency funds for unexpected expenses. Develop action plans to address potential risks proactively.
- Use Fixed-Price Contracts: Fixed-price contracts with suppliers and contractors can limit cost variability and provide financial stability.
- Regular Monitoring and Reporting: Continuously monitor project progress and financial status. Regular reports help identify issues early and facilitate timely interventions.
- Implement Quality Control Measures: Establish stringent quality control procedures to ensure materials and workmanship meet project standards.
- Enhance Communication: Maintain clear and consistent communication with all stakeholders. Transparency helps manage expectations and resolve issues quickly.
- Training and Safety Programs: Invest in training and safety programs to reduce the risk of accidents and health issues on-site.
- Regulatory Compliance Checks: Regularly review and ensure compliance with all legal and regulatory requirements to avoid penalties and project delays.
- Market Analysis: Monitor market conditions and adjust procurement strategies to mitigate the impact of price fluctuations.
Importance of Proactive Risk Management in Quantity Surveying
Proactive risk management is essential in quantity surveying for several reasons. It ensures the project stays within budget and on schedule. By identifying and addressing risks early, quantity surveyors can prevent minor issues from becoming major problems.
Proactive risk management also enhances project quality. Implementing quality control measures and addressing potential issues promptly ensures the final product meets or exceeds client expectations. This approach fosters client trust and satisfaction.
Moreover, proactive risk management contributes to a safer work environment. By investing in training and safety programs, quantity surveyors can reduce the likelihood of accidents and health issues, ensuring the well-being of all workers.
Therefore, risk management is a vital aspect of quantity surveying. Identifying common risks, implementing effective mitigation strategies, and adopting a proactive approach are crucial for controlling costs and ensuring project success.
By prioritizing risk management, quantity surveyors can enhance project outcomes, build client trust, and contribute to the overall success of construction projects.
Read: Student Experiences in Nigerian Polymer Engineering
Life Cycle Costing in Quantity Surveying
Life cycle costing (LCC) is a method used in quantity surveying to assess the total cost of a project over its entire lifespan, from conception to disposal.
It plays a crucial role in cost control by considering not only initial construction costs but also long-term operational and maintenance expenses.
Life Cycle Costing and Its Relevance in Quantity Surveying
Life cycle costing involves evaluating all costs associated with a construction project throughout its life cycle. This includes initial costs, operating costs, maintenance costs, and disposal costs.
Quantity surveyors use LCC to provide a comprehensive financial analysis that guides decision-making and ensures the project remains financially sustainable.
Calculate Life Cycle Costs for Construction Projects
Calculating life cycle costs involves several steps. First, quantity surveyors identify and quantify all relevant costs associated with the project.
They consider costs such as design and construction costs, energy consumption, maintenance expenses, and potential refurbishment or replacement costs over the project’s anticipated lifespan.
Next, quantity surveyors apply present value techniques to adjust future costs to their current value. This step accounts for the time value of money and allows for a fair comparison of costs incurred at different points in time.
Finally, quantity surveyors analyze and interpret the life cycle cost data to inform decision-making. They evaluate alternative design options, materials, and systems to determine which choices offer the best long-term value for the project.
Benefits of Considering Life Cycle Costs in Cost Control Techniques
Considering life cycle costs offers several benefits in cost control techniques. First, it promotes informed decision-making by providing a comprehensive view of the project’s financial implications over time.
This allows stakeholders to make choices that balance initial costs with long-term savings and operational efficiencies.
Second, life cycle costing encourages the selection of sustainable and energy-efficient design solutions.
By evaluating the operational and maintenance costs associated with different design options, quantity surveyors can recommend environmentally friendly choices that minimize life cycle costs.
Third, life cycle costing enhances asset management and planning. It helps stakeholders anticipate future expenses and budget accordingly, reducing the risk of unexpected financial burdens during the project’s life cycle.
This proactive approach improves financial forecasting and ensures financial resources are allocated efficiently.
Moreover, life cycle costing supports risk management by identifying potential cost drivers and vulnerabilities throughout the project’s life cycle. By understanding and mitigating these risks early on, quantity surveyors can minimize the likelihood of cost overruns and project delays.
Conclusion
In summary, effective cost control techniques are essential for achieving success in quantity surveying.
We explored several key techniques that play a crucial role in managing project costs efficiently.
These techniques include value engineering, detailed cost estimation, rigorous project monitoring, and strategic procurement practices.
Each method contributes to ensuring projects remain within budget while maintaining high-quality standards.
Value engineering allows quantity surveyors to optimize costs by finding economical alternatives without compromising on quality.
Detailed cost estimation provides accurate financial forecasts, enabling better budget planning and control.
Rigorous project monitoring helps track progress and identify potential cost overruns early, allowing for timely corrective actions.
Strategic procurement practices ensure that materials and services are acquired at the best possible prices, further enhancing cost efficiency.
Implementing these cost control techniques is vital for managing resources effectively and achieving project goals.
These strategies enhance profitability by minimizing financial risks and ensuring that projects are completed within the allocated budget.
They also play a significant role in ensuring client satisfaction by delivering projects on time and within financial constraints.