Introduction
Advanced welding equipment refers to high-tech tools used for joining metals in Nigeria’s industrial sector. These tools are crucial for ensuring efficiency and quality in welding processes.
Definition of advanced welding equipment
Advanced welding equipment encompasses state-of-the-art machines like robotic welders, laser welders, and automated welding systems. These tools are designed to enhance precision and productivity in welding operations.
Significance of advanced welding equipment in Nigeria’s industrial sector
The use of advanced welding equipment in Nigeria’s industrial sector is essential for improving the overall quality of welded products. This equipment helps in achieving stronger welds, reducing defects, and increasing productivity.
Brief overview of the current state of welding equipment in Nigeria
Currently, Nigeria relies on traditional welding equipment that may not meet the demands of modern industrial processes. There is a need to upgrade to advanced welding equipment to stay competitive in the global market.
Types of Advanced Welding Equipment
In Nigeria’s industrial sector, advanced welding equipment offers diverse technological advancements that revolutionize welding processes across various applications.
Description of Different Types
Several types of advanced welding equipment dominate the market. TIG (Tungsten Inert Gas) welders are renowned for their precision welding capabilities, especially for thin metals. They use a non-consumable tungsten electrode and inert gas shield, ensuring clean welds without splatter.
MIG (Metal Inert Gas) welders are preferred for their versatility and speed in welding thicker materials. They use a consumable wire electrode fed through a welding gun, combined with an inert gas shield. This method is efficient for high-production environments.
Plasma cutters utilize ionized gas to cut through conductive materials swiftly and precisely. These machines offer superior cutting capabilities compared to traditional methods, providing clean edges and reducing post-cutting cleanup.
Benefits and Features
Each type of equipment brings unique benefits. TIG welders excel in welding delicate materials like aluminum and stainless steel, ensuring minimal distortion and superior aesthetics.
MIG welders, on the other hand, enhance productivity with faster deposition rates and less downtime for electrode changes.
Plasma cutters offer versatility by cutting a wide range of materials and thicknesses with ease. Their ability to produce precise cuts and intricate designs makes them indispensable in fabrication and construction projects.
Comparison with Traditional Welding Equipment
Compared to traditional welding equipment, advanced technologies significantly improve efficiency and quality. Traditional methods often involve slower welding speeds and may require multiple passes to achieve desired weld strength.
In contrast, advanced equipment like TIG and MIG welders streamline processes with faster travel speeds and reduced heat input, minimizing distortion and optimizing weld quality.
Moreover, advanced welding equipment enhances operator control and safety. Features such as digital interfaces, automatic settings adjustment, and integrated safety systems improve usability and reduce human error.
This results in higher precision, lower material waste, and increased overall productivity.
Generally, the adoption of advanced welding equipment in Nigeria represents a pivotal advancement in industrial capabilities.
These technologies not only elevate welding precision and efficiency but also contribute to sustainable practices and enhanced safety standards.
Businesses that invest in TIG welders, MIG welders, plasma cutters, and other advanced equipment position themselves for greater competitiveness and growth in a dynamic global market.
Embracing these innovations is crucial for Nigeria’s industrial sector to thrive, meet evolving demands, and achieve sustainable development goals.
Read: Curriculum Overview of Agricultural Engineering Courses
Importance of Upgrading to Advanced Welding Equipment
In Nigeria’s evolving industrial landscape, the significance of upgrading to advanced welding equipment cannot be overstated. This transition offers multifaceted advantages that propel businesses towards enhanced efficiency, superior product quality, and sustainable practices.
Increased efficiency and productivity
Advanced welding technology facilitates faster welding speeds and greater automation capabilities. This streamlines production processes, reduces lead times, and boosts overall productivity.
By leveraging advanced equipment, Nigerian industries can meet growing demands more effectively and capitalize on opportunities for expansion.
Improved quality of welded products
Precision and consistency are hallmarks of advanced welding equipment. These technologies enable welders to achieve tighter control over parameters, resulting in stronger, more reliable welds.
Enhanced product quality not only satisfies stringent industry standards but also enhances customer satisfaction and trust in Nigerian-made products.
Reduction in energy consumption and material wastage
Modern welders are engineered to optimize energy efficiency and minimize the use of consumables. This not only lowers operational costs but also aligns with global sustainability goals.
By reducing energy consumption and material wastage, businesses contribute to environmental conservation while improving their bottom line.
Enhanced safety features for welders
Safety is paramount in welding operations, where workers are exposed to various hazards such as heat, fumes, and electrical risks.
Advanced welding equipment integrates cutting-edge safety features, including automatic shut-off mechanisms, fume extraction systems, and ergonomic designs that mitigate risks and promote a safer working environment.
Prioritizing the health and well-being of welders enhances morale, reduces absenteeism, and fosters a culture of safety within organizations.
Investing in advanced welding technology represents a strategic commitment to competitiveness and sustainability in Nigeria’s industrial sector.
Businesses that embrace these advancements position themselves as industry leaders, capable of delivering high-quality products while maintaining operational efficiency and profitability.
By adopting advanced welding equipment, Nigerian industries not only elevate their technical capabilities but also drive innovation and economic growth.
The ability to meet complex manufacturing demands and adhere to global standards strengthens Nigeria’s position in the international market.
Moreover, these investments pave the way for future advancements in technology and skill development, ensuring long-term viability and resilience against market fluctuations.
In essence, the imperative to upgrade to advanced welding equipment underscores its pivotal role in shaping Nigeria’s industrial future.
Embracing these technologies empowers businesses to achieve operational excellence, sustainability, and safety in welding practices, thereby contributing to a prosperous and competitive industrial landscape.
Read: Agricultural Engineering vs. Other Engineering Fields
Challenges of Adopting Advanced Welding Equipment in Nigeria
When it comes to adopting advanced welding equipment in Nigeria, there are several challenges that have been identified. These challenges hinder the widespread use of advanced technology in the welding industry in the country. Some of the key challenges include:
High initial investment cost
One of the primary challenges faced by companies in Nigeria looking to adopt advanced welding equipment is the high initial investment cost. Advanced welding machines and tools can be quite expensive, making it difficult for smaller businesses to afford them.
Limited availability of advanced welding equipment in local markets
Another major challenge is the limited availability of advanced welding equipment in local markets in Nigeria. This scarcity makes it harder for businesses to access the latest technology and hinders the progress of the welding industry in the country.
Lack of skilled welders trained to operate advanced equipment
Even if companies manage to acquire advanced welding equipment, they often face the challenge of a lack of skilled welders trained to operate these machines effectively. Without proper training, the full potential of the equipment cannot be realized.
Resistance to change from traditional welding methods
Lastly, there is a significant resistance to change from traditional welding methods in Nigeria.
Many welders and companies are comfortable with the techniques they have been using for years and are hesitant to switch to advanced technology, fearing the learning curve and potential risks involved.
Ultimately, while the adoption of advanced welding equipment holds great potential for the welding industry in Nigeria, there are several challenges that need to be addressed.
From high initial costs and limited availability of equipment to a lack of skilled welders and resistance to change, these obstacles must be overcome to fully leverage the benefits of advanced technology in welding.
Read: How to Start a Career in Agricultural Engineering
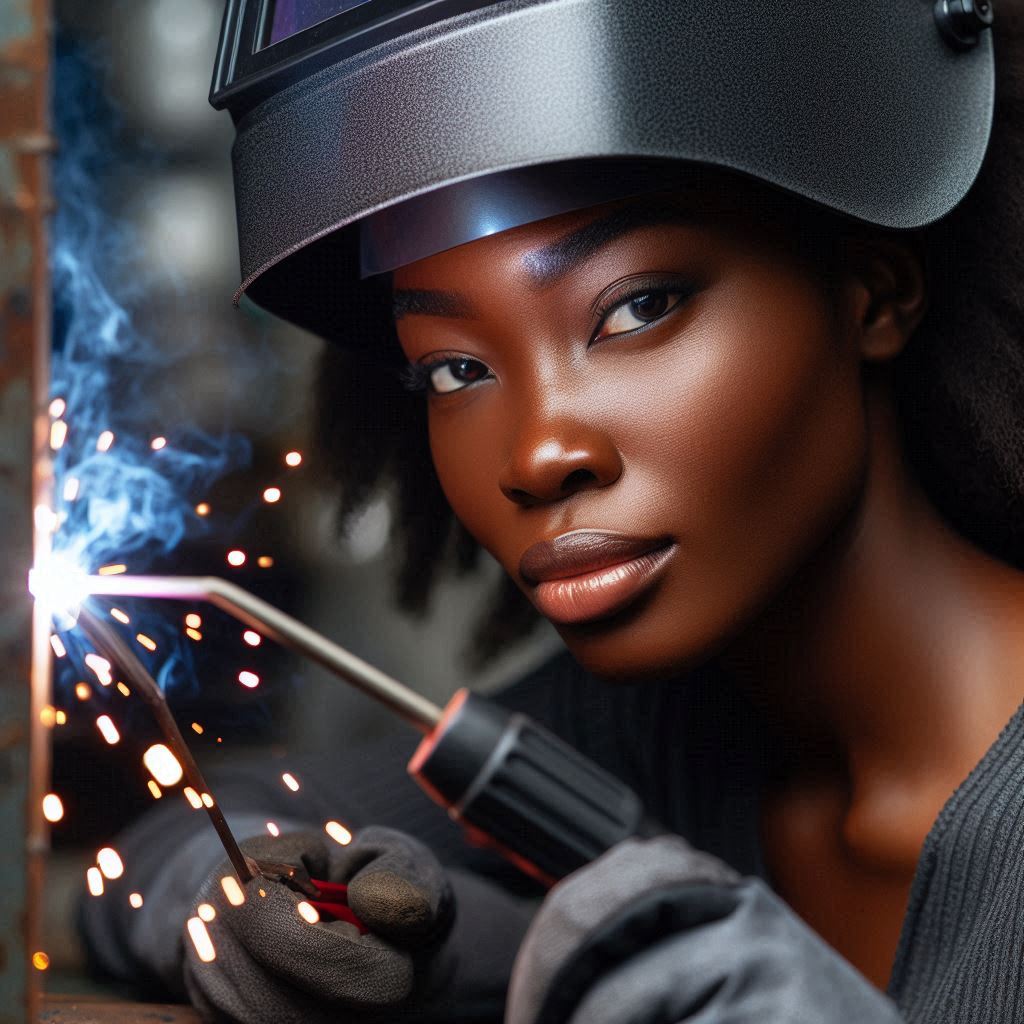
Gain More Insights: Systems Engineering Projects in Nigeria
See Related Content: Polymer and Textile Engineering Conferences in Nigeria
Explore Further: Nigerian Food Engineering: Key Industry Challenges
See Related Content: Nigeria’s Telecom Sector Performance Review
See Related Content: ICT Careers in Nigeria: Prospects and Pathways
Explore Further: Understanding Building Codes and Regulations in Nigeria
Strategies for Overcoming Challenges
When it comes to overcoming challenges in the adoption and utilization of advanced welding equipment in Nigeria, there are several strategies that can be implemented to ensure a smooth transition and maximize the benefits of this technology.
Collaboration between Government, Industry Stakeholders, and Equipment Manufacturers
One key strategy is to foster collaboration between the government, industry stakeholders, and equipment manufacturers.
This collaboration can help in setting standards, regulations, and guidelines for the use of advanced welding equipment. It can also facilitate knowledge sharing and exchange of best practices among the different entities involved in the welding industry.
Investment in Training Programs
Another crucial strategy is to invest in training programs for welders on how to operate advanced equipment. Training programs can help in upskilling and reskilling welders to meet the requirements of using modern welding technology.
By investing in training, businesses can ensure that their workforce is equipped with the necessary skills to operate advanced welding equipment efficiently and effectively.
Financial Incentives and Subsidies
Providing financial incentives and subsidies to encourage businesses to invest in advanced welding technology is an effective strategy to overcome challenges.
By offering tax incentives, grants, or subsidies, the government can incentivize businesses to adopt advanced welding equipment.
This can help in offsetting the initial costs associated with purchasing and implementing advanced technology and make it more affordable for businesses to invest in such equipment.
Transform Your Career with Expert Guidance
Get personalized mentorship consulting that’s tailored to your unique path. Our expert advice is actionable and exclusive.
Get StartedImportation and Localization
Another strategy is to focus on the importation and localization of advanced welding equipment to improve accessibility.
By importing advanced equipment from established manufacturers, businesses can gain access to cutting-edge technology that may not be readily available in the local market.
Additionally, efforts can be made to localize the production of advanced welding equipment within Nigeria. This can help in reducing costs, improving availability, and promoting the growth of the local manufacturing industry.
In fact, overcoming challenges in the adoption and utilization of advanced welding equipment in Nigeria requires a multi-faceted approach.
By implementing strategies such as collaboration, investment in training programs, providing financial incentives, and focusing on importation and localization.
Businesses and the welding industry as a whole can harness the full potential of advanced welding technology and drive growth and innovation in the sector.
Read: Top Universities for Agricultural Engineering in Nigeria
Case Studies of Successful Implementation
In Nigeria, several pioneering companies have embraced advanced welding equipment, revolutionizing their operations and achieving remarkable growth.
Highlighting Successful Companies
One standout example is Naija Welding Solutions., a leading fabrication company in Lagos.Naija Welding Solutions invested in state-of-the-art TIG welders and plasma cutters to enhance their manufacturing capabilities.
These investments enabled them to undertake complex projects with precision and efficiency.
Impact on Operations and Product Quality
The adoption of advanced equipment has significantly elevated product quality at Naija Welding Solutions .
Their TIG welders ensure clean, strong welds on stainless steel components, meeting stringent client specifications. Plasma cutters have streamlined their cutting processes, delivering precise cuts and reducing material waste.
Business Growth and Competitive Edge
Naija Welding Solutions Engineering’s strategic investment in advanced welding technology has bolstered their competitive edge in the market.
They now offer quicker turnaround times, adhere to higher quality standards, and attract more lucrative contracts. This has resulted in substantial business growth and enhanced profitability.
Examples of Cost Savings and Efficiency Gains
Another success story is NigerWeld Manufacturing Ltd., based in Port Harcourt, which implemented MIG welders and automated welding systems.
These advancements have slashed production costs by reducing labor expenses and minimizing material wastage. NigerWeld Manufacturing Ltd now produces more units in less time, driving up overall efficiency.
Improved Safety Measures
Advanced welding equipment has also improved safety measures at these companies. Integrated safety features such as automatic shutdown systems and enhanced ventilation have reduced workplace accidents and improved employee well-being.
This focus on safety not only protects personnel but also enhances overall operational continuity.
Essentially, the case studies of Naija Welding Solutions Engineering and NigerWeld Manufacturing Ltd illustrate the transformative impact of advanced welding equipment in Nigeria’s industrial sector.
These companies have leveraged technology to enhance operational efficiency, elevate product quality, and achieve significant cost savings.
By embracing innovation, they have secured a competitive advantage, driving sustainable business growth and contributing to Nigeria’s industrial advancement.
As more companies follow suit, the adoption of advanced welding equipment will continue to shape a prosperous and resilient industrial landscape in Nigeria.
Explore Further: Economic Benefits of Wood Production Engineering
Find Out More: Roles and Responsibilities of Quantity Surveyors
See Related Content: Skills Required for Computer Engineering in Nigeria
Discover More: Smartphone Penetration in Nigeria
Conclusion
As we conclude, the integration of advanced welding equipment stands as a transformative force in Nigeria’s industrial evolution.
The discussion has underscored how modern welding technologies enhance efficiency, precision, and safety across diverse sectors.
By embracing these advancements, Nigerian industries can bolster productivity, reduce operational costs, and deliver higher-quality outputs.
The importance of investing in upgraded welding equipment cannot be overstated.
It not only improves competitiveness but also ensures long-term sustainability in a rapidly advancing global market.
Businesses that prioritize equipment modernization position themselves for growth and resilience against technological obsolescence.
Moreover, the adoption of advanced welding equipment fosters innovation and supports economic development.
It enables businesses to meet evolving industry standards and customer expectations effectively.
Therefore, I encourage businesses across Nigeria to seize the opportunity to upgrade their welding capabilities.
By doing so, they not only enhance operational efficiency but also contribute to the overall advancement and competitiveness of Nigeria’s industrial sector.