Introduction
Welding is a process of joining two materials together using heat, pressure, or a combination of both. It is crucial in various industries such as construction, manufacturing, and automotive.
Overview of Common Welding Materials in Nigeria
In Nigeria, the most common welding materials include electrodes, shielding gases, and filler metals. These materials are essential for ensuring strong and durable welds in various projects.
Electrodes
Electrodes are used in arc welding processes to create an electrical arc that melts the base metal and filler material. In Nigeria, electrodes come in different types such as coated electrodes for different welding applications.
Shielding Gases
Shielding gases, such as argon and CO2, are used to protect the weld pool from atmospheric contamination during welding. In Nigeria, these gases are commonly used in gas metal arc welding (GMAW) and gas tungsten arc welding (GTAW) processes.
Filler Metals
Filler metals are used to fill the gap between the two materials being welded together. In Nigeria, common filler metals include steel, stainless steel, and aluminum alloys, depending on the type of base metal being welded.
In summary, understanding the common welding materials used in Nigeria is essential for producing high-quality welds in various industries.
By using the right materials and techniques, welders can ensure that their projects are strong, durable, and meet industry standards.
Overview of Commonly Used Welding Materials in Nigeria
In Nigeria, welding is a crucial skill employed across various industries, necessitating a deep understanding of different welding materials. Each material possesses distinct properties that influence its suitability for specific applications.
Mild Steel
- Properties: Mild steel is abundant and affordable, characterized by its low carbon content, making it easy to weld and shape. It exhibits good strength and ductility.
- Benefits: Widely available in Nigeria, mild steel is versatile and suitable for a wide range of welding applications, from construction to automotive industries.
- Drawbacks: It is prone to corrosion without proper protection and lacks the corrosion resistance of stainless steel.
Stainless Steel
- Properties: Stainless steel offers excellent corrosion resistance due to its chromium content. It is durable, strong, and retains its strength at high temperatures.
- Benefits: Ideal for environments prone to corrosion, such as coastal regions or chemical plants. It maintains a polished appearance.
- Drawbacks: More expensive than mild steel, stainless steel requires expertise to weld properly and is more prone to distortion.
Aluminum
- Properties: Aluminum is lightweight, with good conductivity and corrosion resistance. It is commonly alloyed with other metals to enhance strength.
- Benefits: Used extensively in aerospace, marine, and automotive industries in Nigeria due to its lightweight properties and resistance to rust.
- Drawbacks: Aluminum welding requires specific techniques and equipment due to its low melting point and tendency to form oxide layers.
Cast iron
- Properties: Cast iron is brittle and has high compressive strength. It retains its shape under stress and is resistant to deformation.
- Benefits: Suitable for applications requiring high strength and wear resistance, such as engine blocks and machinery components.
- Drawbacks: Cast iron is challenging to weld due to its high carbon content, which can lead to cracking and brittleness if not properly managed.
Selecting the appropriate welding material in Nigeria depends on several factors, including the application, environmental conditions, and budget constraints.
For general construction and fabrication, mild steel remains a popular choice due to its affordability and versatility.
However, in corrosive environments or where aesthetics are important, stainless steel offers superior performance despite its higher cost.
Aluminum finds its niche in industries requiring lightweight structures and excellent corrosion resistance, such as the maritime and aerospace sectors.
Cast iron, although challenging to weld, serves critical roles in heavy machinery and automotive components where strength and durability are paramount.
Understanding the properties, benefits, and drawbacks of commonly used welding materials in Nigeria is essential for achieving successful welds and ensuring the longevity of welded structures.
Each material offers unique advantages that cater to specific application requirements, highlighting the importance of informed material selection in welding projects across various industries in Nigeria.
Read: Systems Engineering for Nigerian Public Sector Projects
Availability and accessibility of welding materials in Nigeria
When it comes to the availability and accessibility of welding materials in Nigeria, welders face various challenges in sourcing these essential materials both in local markets and online platforms. Here is a detailed overview:
Availability of Welding Materials in Local Markets
- In Nigeria, local markets play a crucial role in providing welding materials to welders across the country.
- Local markets are abundant with various types of welding materials such as electrodes, filler metals, fluxes, and protective gear.
- Welders can easily access these materials in markets located in major cities like Lagos, Abuja, Port Harcourt, and Kano.
- There is a wide range of choices available in terms of brands and quality of welding materials in local markets.
- Local vendors and suppliers offer competitive prices for welding materials, making them affordable for welders with different budget constraints.
Accessibility of Welding Materials on Online Platforms
- With the advent of e-commerce in Nigeria, online platforms have become increasingly popular among welders for sourcing welding materials.
- Platforms like Jumia, Konga, and Alibaba offer a wide selection of welding materials that can be purchased with just a few clicks.
- Welders can compare prices, read reviews, and choose from different brands without leaving the comfort of their homes or workshops.
- Online platforms provide convenience and flexibility in purchasing welding materials, especially for welders located in remote areas.
Challenges Faced by Welders in Sourcing Materials in Nigeria
- One of the major challenges faced by welders in Nigeria is the inconsistency in the availability of specific welding materials.
- Some welding materials may be scarce or in high demand, leading to shortages in local markets and delays in project completion.
- Welders often encounter counterfeit or substandard welding materials in the market, which can compromise the quality of their work.
- Price fluctuations in welding materials can also pose a challenge for welders, impacting their budget planning and project estimates.
- Limited access to specialized welding materials or equipment in Nigeria can hinder welders from taking on complex or high-tech welding projects.
In general, while welders in Nigeria have various options for sourcing welding materials through local markets and online platforms, they still face challenges such as availability issues, counterfeit products, price fluctuations, and limited access to specialized materials.
It is essential for welders to stay informed, research thoroughly, and choose trusted suppliers to ensure they have access to high-quality welding materials for their projects.
Read: Comparing Systems Engineering Programs in Nigeria
Cost considerations of welding materials in Nigeria
In Nigeria, the cost of welding materials is a significant factor that welders need to consider.
Understanding the cost factors influencing the price of welding materials in the Nigerian market can help welders make informed decisions and save money on their purchases.
Cost Factors Influencing the Price of Welding Materials in Nigeria
- Currency Exchange Rates: The fluctuation in currency exchange rates can have a direct impact on the cost of welding materials in Nigeria. As the value of the Naira changes against other currencies, the prices of imported welding materials can vary.
- Import Duties and Taxes: Import duties and taxes imposed on welding materials can increase their overall cost. These additional charges are passed on to the consumers, making imported welding materials more expensive.
- Transportation Costs: The cost of transporting welding materials from the point of entry to the end-user can also affect their price. High transportation costs, especially in remote areas, can drive up the overall cost of welding materials.
- Supply and Demand: The law of supply and demand plays a crucial role in determining the price of welding materials in Nigeria. If the demand for a particular type of welding material exceeds its supply, prices are likely to increase.
- Brand and Quality: The brand and quality of welding materials can also impact their price. Premium brands and high-quality materials tend to come with a higher price tag, reflecting their durability and performance.
Tips on Saving Money on Purchasing Welding Materials in Nigeria
- Buy in Bulk: Purchasing welding materials in bulk can often lead to discounts or lower prices per unit. Welders can consider pooling their resources with other welders to make bulk purchases.
- Comparison Shopping: It is essential for welders to compare prices from different suppliers before making a purchase. This can help them identify the best deals and save money on welding materials.
- Look for Discounts and Promotions: Keep an eye out for discounts, promotions, and sales events offered by welding material suppliers. Taking advantage of these opportunities can lead to significant cost savings.
- Consider Local Alternatives: Instead of relying solely on imported welding materials, explore locally produced alternatives. Local suppliers may offer competitive prices and quality products that can help reduce costs.
- Maintain and Care for Equipment: Proper maintenance and care of welding equipment can extend its lifespan and reduce the need for frequent replacements. This can result in long-term cost savings on welding materials.
By understanding the cost factors influencing the price of welding materials in Nigeria and implementing cost-saving strategies, welders can effectively manage their expenses and optimize their welding operations.
Read: Benefits of Studying Systems Engineering in Nigeria
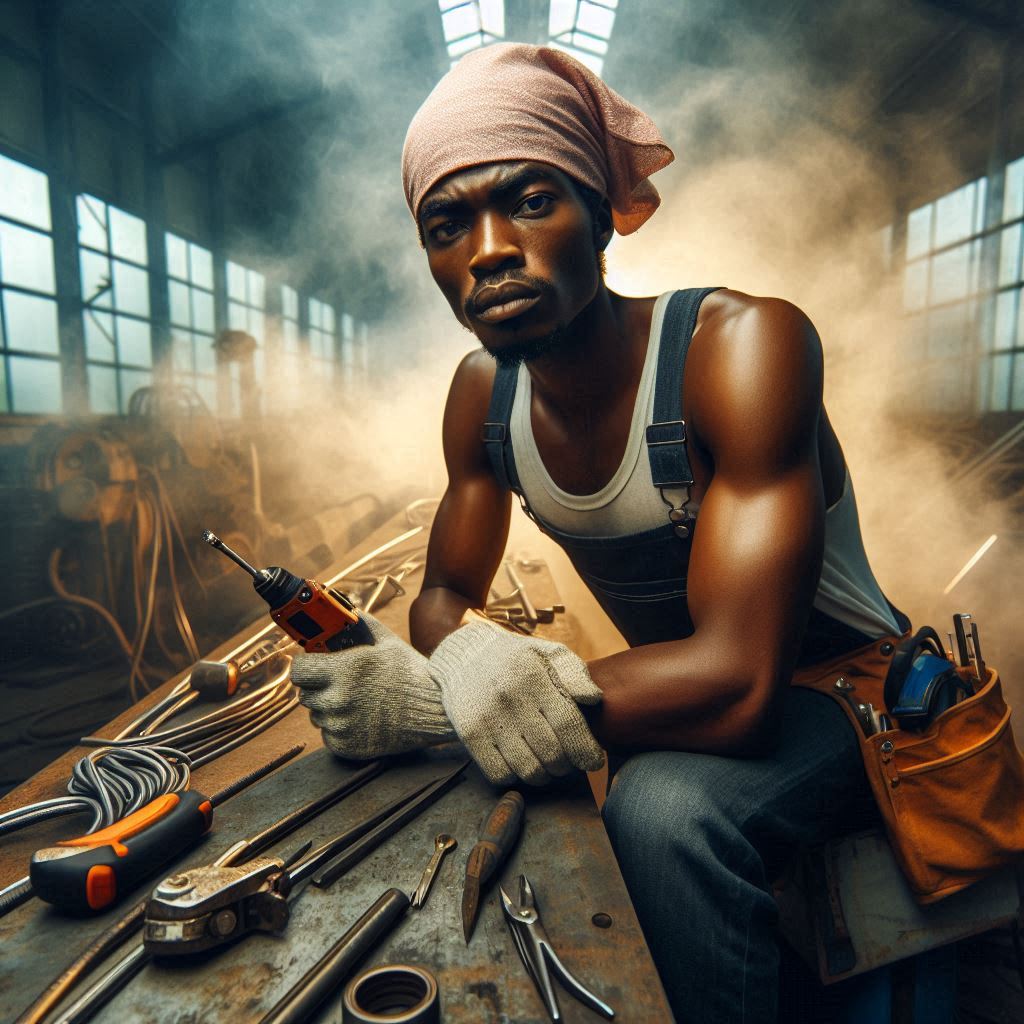
Discover More: Career Pathways in Nigerian Software Engineering
Quality Control and Standards for Welding Materials in Nigeria
Quality control measures for welding materials are crucial to ensure safety and reliability in construction and industrial projects across Nigeria. Consistency and reliability in welding materials directly impact the structural integrity and longevity of welded joints.
Importance of Quality Control Measures
Quality control in welding materials guarantees that the materials used meet specified standards and are suitable for their intended applications.
It involves rigorous testing and inspection processes to detect any defects or inconsistencies that could compromise weld quality.
Ensuring the quality of welding materials helps in preventing weld failures, which can lead to costly repairs, project delays, and even safety hazards.
By adhering to strict quality control measures, welders and engineers can have confidence in the materials they use, thus enhancing overall project reliability.
Relevant Standards and Certifications
In Nigeria, welding materials should conform to international standards such as those set by the International Organization for Standardization (ISO) and the American Welding Society (AWS).
These standards define requirements for material composition, mechanical properties, and manufacturing processes.
ISO 9001 certification is widely recognized and ensures that manufacturers follow stringent quality management systems.
It provides assurance that welding materials are produced under controlled conditions and meet specified quality criteria.
Nigerian Industrial Standards (NIS)
The Standards Organization of Nigeria (SON) oversees the adoption and implementation of Nigerian Industrial Standards (NIS) for welding materials.
These standards are tailored to local environmental conditions and regulatory requirements, ensuring compatibility with Nigerian construction practices.
Testing and Inspection Procedures
Before welding materials are used in construction projects, they undergo various testing procedures.
These include chemical analysis, mechanical testing (such as tensile and impact tests), and non-destructive testing (NDT) methods like ultrasonic testing and radiographic inspection.
Each batch of welding materials should be accompanied by a test certificate that verifies compliance with specified standards.
Welders and inspectors rely on these certificates to confirm the quality and suitability of materials for welding applications.
Role of Welding Material Suppliers
Suppliers play a crucial role in maintaining quality control by sourcing materials from reputable manufacturers with proven track records.
They ensure that materials are stored and transported under proper conditions to prevent contamination or degradation.
Regular audits and inspections of welding material suppliers help to verify adherence to quality standards and consistency in product quality.
This proactive approach minimizes risks associated with substandard materials and reinforces the reliability of weld joints.
In fact, quality control measures for welding materials in Nigeria are essential for upholding construction standards and ensuring project success.
By adhering to international and local standards, implementing rigorous testing procedures, and working with reliable suppliers, stakeholders can mitigate risks and achieve superior weld quality.
This commitment to excellence not only enhances structural integrity but also fosters a culture of safety and reliability in welding practices across the nation.
Read: Systems Engineering and Nigerian Tech Startups
Gain More Insights: Wood Production Engineering: Community Impact
Explore Further: Challenges in Nigerian Software Engineering
Environmental impact of welding materials in Nigeria
The environmental concerns associated with welding materials
When it comes to the environmental impact of welding consumables in Nigeria, there are several concerns that need to be addressed.
Welding processes can have both short-term and long-term effects on the environment, including air and water pollution, energy consumption, and waste generation.
Air Pollution
One of the major concerns with welding consumables is the release of fumes and gases into the air during the welding process.
These fumes can contain hazardous substances like heavy metals, ozone-depleting chemicals, and volatile organic compounds.
When inhaled, these pollutants can have adverse effects on human health and contribute to air pollution.
Water Pollution
Another issue related to welding consumables is the potential for water pollution. Improper disposal of welding waste, such as metal shavings, slag, and cleaning chemicals, can contaminate water sources and harm aquatic ecosystems.
Additionally, runoff from welding sites can carry pollutants into rivers, lakes, and groundwater, posing a threat to both wildlife and human health.
Energy Consumption
Welding processes typically require a significant amount of energy, especially in industrial settings where large-scale welding is done.
The energy used to power welding equipment contributes to greenhouse gas emissions and puts a strain on local energy resources.
Finding ways to reduce energy consumption during welding can help mitigate its environmental impact.
Waste Generation
Welding activities generate various types of waste, including scrap metal, used electrodes, packaging materials, and wastewater.
Improper handling and disposal of this waste can lead to land pollution and contamination of soil and groundwater.
It is essential to implement proper waste management practices to minimize the environmental impact of welding consumables.
Eco-Friendly Alternatives
To reduce the environmental impact of welding consumables in Nigeria, there are several eco-friendly alternatives and practices that can be adopted:
- Choose low-emission welding techniques such as gas metal arc welding (GMAW) or shielded metal arc welding (SMAW) to minimize air pollution.
- Use environmentally friendly welding consumables, such as low-hydrogen electrodes and water-based cleaning solutions, to reduce toxic emissions.
- Implement recycling programs for metal scrap and other waste generated during welding to minimize landfill waste and conserve resources.
- Invest in energy-efficient welding equipment and technologies to reduce energy consumption and carbon footprint.
- Train welders on proper waste management practices and environmental regulations to ensure compliance and minimize negative impacts on the environment.
- Collaborate with regulatory agencies, industry partners, and local communities to develop sustainable practices and initiatives that promote environmental stewardship in the welding sector.
By embracing eco-friendly alternatives and practices, the welding industry in Nigeria can reduce its environmental footprint and contribute to a cleaner and healthier environment for future generations.
Discover More: Common Myths About Petroleum Engineering in Nigeria
Transform Your Career with Expert Guidance
Get personalized mentorship consulting that’s tailored to your unique path. Our expert advice is actionable and exclusive.
Get StartedDiscover More: Career Opportunities in Nigeria’s Glass Technology Field
Delve into the Subject: Career Paths for Civil Engineering Graduates in Nigeria
Find Out More: How to Start a Structural Engineering Firm in Nigeria
Conclusion
In this blog section, we explored the significance of welding consumables in Nigeria. We discussed various types of materials commonly used in welding processes across the country.
Understanding the importance of quality welding consumables is crucial for ensuring safety, efficiency, and durability in welding projects.
Key Points Discussed
Quality welding consumables such as electrodes, filler metals, and protective gear are essential for safe and efficient welding practices.
These materials play a critical role in achieving strong and durable welds that can withstand various environmental conditions.
The availability and sourcing of welding consumables in Nigeria can impact project timelines and costs.
It is essential for welders and fabricators to have reliable access to high-quality materials to maintain consistency and quality in their work.
Different welding processes require specific materials tailored to the type of metal being welded and the environmental conditions.
Understanding these requirements helps in selecting the right materials for each project, ensuring optimal results.
Significance of Using Quality Welding Materials
Using quality welding consumables is paramount for ensuring safety during welding operations. Inferior materials can lead to weld defects, compromising structural integrity and posing safety risks to welders and the public.
Efficiency in welding operations is greatly influenced by the quality of materials used.
High-quality electrodes and filler metals contribute to smoother welding processes, reducing downtime and enhancing productivity.
Durability of welded structures depends on the quality of materials used.
Proper selection of welding consumables ensures that welds are strong and resistant to corrosion and other forms of degradation, thereby prolonging the lifespan of welded components.
Emphasis on Safety, Efficiency, and Durability
The safety of welders and the general public should always be a top priority in welding projects.
By using quality materials, welders can minimize the risks associated with welding operations, such as exposure to hazardous fumes and potential accidents due to weld failures.
Efficiency in welding not only reduces project timelines but also optimizes resource utilization.
High-quality welding consumables contribute to smoother workflow and better utilization of manpower and equipment.
Durability is essential for ensuring that welded structures and components withstand the test of time and environmental factors.
Quality welding consumables contribute significantly to the longevity and reliability of welds, reducing maintenance costs and enhancing overall project sustainability.
In closing, the choice of welding consumables in Nigeria directly impacts the safety, efficiency, and durability of welding projects.
By prioritizing the use of high-quality materials and adhering to best practices, welders can achieve superior results that meet both technical and safety standards.