Introduction
Metal work technology involves the fabrication, welding, and shaping of metal materials for various applications.
It plays a crucial role in industries such as manufacturing, construction, and automotive.
The field requires a set of essential tools that are vital for ensuring precision, efficiency, and safety in metalworking processes.
Essential tools are the backbone of metal work technology as they enable students to perform tasks with accuracy and effectiveness.
Without these tools, students would struggle to achieve the desired results in their projects.
The right tools not only help in enhancing productivity but also ensure the quality of the final output.
Essential tools such as welding machines, angle grinders, drills, and measuring instruments are indispensable in metal work technology.
Welding machines are crucial for joining metal components, while angle grinders help in shaping and polishing metal surfaces.
Drills are essential for creating holes in metal materials, and measuring instruments like calipers and rulers are vital for ensuring precise measurements.
In essence, essential tools are the foundation of metal work technology, allowing students to explore their creativity and skills in working with metal.
By having access to a wide array of tools, students can master different techniques and processes in metalworking, leading to successful projects and career opportunities in various industries.
It is essential for metal work technology students to familiarize themselves with these tools and learn how to use them effectively to achieve excellence in their craft.
Safety Tools
When it comes to metal work projects, safety should always be the top priority for students.
Safety tools not only protect students from accidents and injuries but also create a secure environment for learning and practicing metal work skills.
Safety Goggles
These safety goggles are a crucial tool for metal work technology students as they protect the eyes from sparks, debris, and harmful fumes.
Wearing safety goggles can prevent eye injuries and ensure clear vision while working with metal materials.
Students should always wear safety goggles that meet the required safety standards for maximum protection.
Gloves
Gloves are essential in metal work projects to protect the hands from sharp edges, hot surfaces, and potential cuts or burns.
By wearing gloves, students can maintain a secure grip on tools and materials, reducing the risk of accidents.
It is important for students to choose the right type of gloves based on the specific requirements of the project.
Aprons
Aprons play a significant role in keeping students’ clothing safe from sparks, stains, and other hazards during metal work activities.
By wearing aprons, students can protect their clothes from damage and maintain a professional appearance in the workshop.
Students should opt for durable and flame-resistant aprons that provide adequate coverage and comfort.
Following safety protocols is equally important to ensure a safe working environment for metal work technology students.
It is crucial for students to adhere to safety guidelines and regulations to prevent accidents and injuries.
By incorporating safety tools such as goggles, gloves, and aprons into their metal work projects, students can minimize risks and focus on honing their skills effectively. Remember, safety first, always!
Read: Latest Developments in Woodwork Technology Nigeria
Cutting Tools
Essential cutting tools
- Hacksaws: Hacksaws are essential cutting tools for metal work technology students.
They are handheld saws with a thin blade used for cutting metal materials. - Shears: Shears are another important cutting tool in metal work technology. They are designed to cut straight lines in metal sheets and plates.
- Angle Grinders: Angle grinders are versatile cutting tools that are commonly used in metal work projects.
They can be used for cutting, grinding, and polishing metal materials.
How these tools are used:
Hacksaws are typically used for making intricate cuts and shaping metal rods and pipes. They require manual effort to operate but offer precision in cutting.
Shears are perfect for cutting large pieces of metal sheets or plates.
They have sharp blades that can easily slice through the material, making them ideal for straight cuts.
Angle grinders, on the other hand, are power tools that use a rotating abrasive disc to cut through metal.
They are versatile and can be used for various cutting tasks in metal work projects.
Overall, these cutting tools play a crucial role in the fabrication process for metal work technology students.
They enable students to accurately cut and shape metal materials to create intricate designs and structures for their projects.
Mastering the use of these tools is essential for success in the field of metal work technology.
Read: Nigerian Metal Work Technology: Job Market Trends
Measuring Tools
Metal work projects require precision in measurements to ensure accurate results and successful outcomes.
Importance of Precise Measurements
Accurate measurements are crucial in metal work as even the smallest error can lead to faulty products or structures.
Tape Measure
A tape measure is a versatile tool that allows metal work students to quickly and easily measure long distances.
It is essential for tasks such as measuring the length of metal rods or determining the dimensions of a project.
Transform Your Career with Expert Guidance
Get personalized mentorship consulting that’s tailored to your unique path. Our expert advice is actionable and exclusive.
Get StartedCalipers
Calipers are precision measuring tools used to accurately gauge the thickness or diameter of metal components.
They come in various types such as Vernier, Digital, or Dial calipers, each suitable for specific measurement needs.
Combination Squares
Combination squares are multipurpose tools that allow students to measure, mark, and check for squareness in metal work projects.
They consist of a ruler and a head with a level, square, or protractor, enabling precise and repeatable measurements.
Using these measuring tools, metal work technology students can achieve accurate results in their projects and ensure the quality and integrity of their work.
Read: Woodwork Technology: Nigerian Certification Process
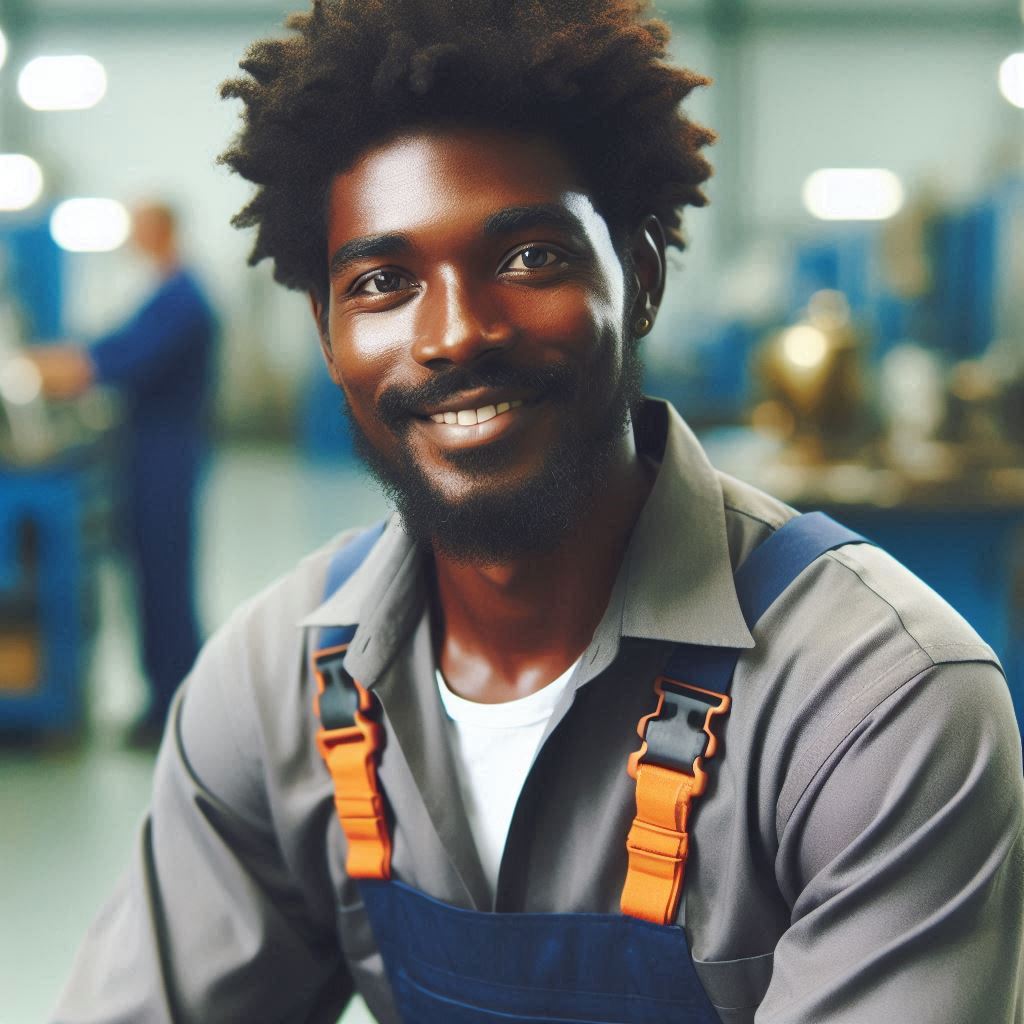
See Related Content: How Biology Education Contributes to Healthcare
Joining Tools
When it comes to metal work technology, joining tools play a crucial role in creating strong and durable metal structures.
Welding machines, soldering irons, and rivet guns are essential tools that every metal work student should be familiar with.
Importance of Welding Machines, Soldering Irons, and Rivet Guns
Welding machines are used to join metal pieces together by melting the materials and fusing them into a single piece.
Versatile tools create butt, lap, and corner joints, offering various construction options.
Welding is a common method used in industries such as construction, automotive, and aerospace.
Soldering irons join metal by melting solder and applying it to joints.
Soldering is often used in electronics and plumbing applications where a strong, yet more delicate bond is required.
It is important to choose the right soldering iron based on the type of material you are working with and the required temperature for the solder to melt effectively.
Rivet guns fasten metal by inserting rivets through holes and deforming their ends.
Riveting, a popular choice in industries, joins metals cost-effectively and reversibly, crucial for disassembly needs in aircraft and ship manufacturing.
Different Methods of Joining Metal Materials and Tools Required
Welding
There are several types of welding techniques used in metal work technology. Some common methods include:
- Gas Metal Arc Welding (GMAW)
- Gas Tungsten Arc Welding (GTAW)
- Shielded Metal Arc Welding (SMAW)
Each welding technique requires specific welding machines, such as MIG welders for GMAW, TIG welders for GTAW, and stick welders for SMAW.
It is important to choose the right welding machine based on the thickness of the materials being joined and the type of joint required.
Soldering
When it comes to soldering, the type of soldering iron you use will depend on the material you are working with and the soldering technique you are using.
Some common soldering techniques include:
- Surface Mount Technology (SMT)
- Through-Hole Technology (THT)
- Hot Bar Soldering
Selecting the correct soldering iron tip size and temperature depends on component size and solder type.
Using the wrong soldering iron can result in poor joint quality and damage to the components being soldered.
Riveting
Riveting requires a rivet gun and the appropriate rivets for the job.
There are different types of rivets, including solid, tubular, and blind rivets, each suited for specific applications.
The size and material of the rivet should be chosen based on the thickness of the materials being joined and the required strength of the joint.
Choosing the right joining tools and techniques is essential in metal work technology to ensure strong, reliable, and safe metal structures.
By understanding the importance of welding machines, soldering irons, and rivet guns, students can master the art of joining metal materials effectively and efficiently.
Read: Metal Work Technology: Nigerian Industry Demands
Shaping Tools
Role of shaping tools like hammers, mallets, and files in metal work projects
Shaping tools like hammers, mallets, and files are indispensable in metal work projects. They enable precise manipulation of metal materials.
Hammers deliver controlled force, shaping metals effectively. Mallets provide softer impacts, ideal for delicate shaping.
Files refine surfaces with precision, ensuring smooth finishes.
These tools facilitate intricate detailing in metal work. They empower students to sculpt metals into desired forms.
How these tools help students form metal materials into desired shapes and structures
Hammers forge metals through controlled strikes, molding them into various shapes. Mallets complement hammers, offering gentler shaping for intricate designs.
Files refine metal surfaces, smoothing imperfections and edges. They allow students to achieve precise dimensions and smooth finishes.
Students utilize hammers to shape metal sheets into three-dimensional forms. Mallets aid in bending and shaping metals without causing damage.
Files are crucial for finishing touches, ensuring surfaces are smooth and polished. They refine intricate details, enhancing the overall quality of metal work.
In a nutshell, shaping tools are indispensable for metal work students. They play a vital role in shaping metals into desired structures, fostering creativity and precision.
See Related Content: Top Universities for Computer Science in Nigeria
Conclusion
Essential tools are vital for metal work technology students. Investing in quality tools ensures successful outcomes.
Proper training with these tools is also crucial for achieving excellence in the field.
It is important to understand the significance of having the right tools to perform tasks efficiently and accurately in metalwork technology.
Students should prioritize acquiring these tools to enhance their skills and expertise for future career opportunities.
By having a comprehensive and well-equipped toolbox, students can take on various metalwork projects with confidence and precision.
Ultimately, the combination of essential tools and proper training is essential for students to excel in the metalwork technology industry.