Introduction
Overview of the current state of welding technology in Nigeria
Welding technology in Nigeria stands at a pivotal juncture, reflecting both challenges and opportunities in its current state.
Across various industries, the importance of welding cannot be overstated, serving as a cornerstone for infrastructure development and industrial growth.
Currently, welding in Nigeria faces significant challenges despite its crucial role. Infrastructure gaps and limited access to advanced equipment hamper efficiency and quality. Training and skill development also lag, affecting overall industry standards.
Infrastructure deficiencies pose obstacles to welding advancements.
Outdated machinery and inadequate facilities hinder productivity and quality. Limited availability of modern welding tools constrains the industry’s ability to meet international standards.
A critical aspect needing attention is the training of welders. Skill development programs are sporadic, with a shortage of certified instructors.
This gap not only affects quality but also restricts innovation and adaptation of new technologies.
Importance of Welding Technology in Industries
Welding technology plays a vital role across diverse industries in Nigeria.
From construction to manufacturing, its applications are fundamental for creating robust and durable structures. Industries rely on welding for assembly, repair, and maintenance, essential for operational continuity.
In the construction sector, welding is indispensable for erecting buildings, bridges, and infrastructure projects.
Proper welding techniques ensure structural integrity and longevity, crucial for sustainable development and urban expansion.
Manufacturing industries heavily depend on welding for assembling components and fabricating machinery.
Precision welding techniques enhance product quality, reliability, and operational efficiency, contributing to competitiveness in the global market.
The oil and gas industry relies on welding for pipeline construction, maintenance, and repairs.
High standards in welding are imperative for ensuring safety, environmental protection, and operational reliability in this critical sector.
Despite challenges, advancements in welding technology offer promise for Nigeria’s industrial growth.
Innovations such as automated welding systems and advanced materials enhance efficiency, precision, and safety in welding processes.
Future Prospects and Opportunities
Looking ahead, the future of welding technology in Nigeria holds vast opportunities. Investment in infrastructure, modern equipment, and comprehensive training programs can elevate industry standards.
Collaboration with international partners for knowledge exchange and technology transfer is also pivotal.
Essentially, welding technology in Nigeria is pivotal for industrial development across various sectors.
Addressing current challenges through infrastructure improvement, skills development, and embracing technological innovations will pave the way for a robust and competitive welding industry.
As Nigeria strives for economic growth and sustainability, investing in welding technology emerges as a strategic imperative for the nation’s industrial future.
Current Challenges in Welding Technology in Nigeria
When it comes to the future of welding technology in Nigeria,
it is crucial to first take a look at the current challenges that the industry is facing.
These challenges play a significant role in shaping the direction that welding technology will take in the country. Some of the prominent challenges include:
Lack of Skilled Welders and Technicians
One of the primary challenges facing the welding industry in Nigeria is the shortage of skilled welders and technicians.
With the increasing demand for welding services across various sectors,
there is a pressing need for well-trained professionals who can deliver high-quality welding work.
Unfortunately, the country is facing a deficit in skilled welders, which hinders the growth and development of the industry.
Poor Infrastructure and Outdated Equipment
Another major challenge that the welding industry in Nigeria is grappling with is poor infrastructure and outdated equipment.
Many welding workshops and facilities in the country lack the necessary infrastructure and modern equipment required to carry out complex welding projects efficiently.
This not only affects the quality of work produced but also hampers the overall productivity and competitiveness of the industry.
Limited Access to Advanced Welding Technology
In today’s rapidly evolving technological landscape, access to advanced welding technology is essential for the industry to thrive. However, in Nigeria, limited access to cutting-edge welding technologies poses a significant challenge.
Without access to the latest welding equipment, tools, and techniques, welders in the country struggle to keep pace with global standards and best practices.
This ultimately hinders the industry’s ability to innovate and compete on a global scale.
Basically, addressing these current challenges is crucial for the future growth and sustainability of the welding industry in Nigeria.
By investing in skill development, improving infrastructure,
and providing access to advanced welding technology, the country can overcome these obstacles and propel the industry towards a brighter future.
Read: Role of ICT in Nigerian Telecommunication Engineering
Opportunities for Advancement in Welding Technology
In Nigeria, the welding technology sector is poised for significant growth and advancement.
As the country continues to develop its infrastructure and industrial capabilities, there are numerous opportunities for skilled welders to thrive. Let’s explore some of the key opportunities for advancement in welding technology:
Growing demand for skilled welders in various industries
- The demand for skilled welders in Nigeria is on the rise, particularly in industries such as construction, oil and gas, automotive, and manufacturing.
- As these industries expand and modernize, the need for qualified welders who can work with advanced welding technologies will only increase.
- Welders who stay current with the latest welding techniques and equipment will be in high demand and will have numerous opportunities for career advancement.
- With the right skills and experience, welders can pursue higher-paying jobs, leadership positions, and even start their own welding businesses.
Potential for collaboration with international companies for technology transfer
- Nigeria has the opportunity to collaborate with international companies in the welding technology sector to facilitate technology transfer and knowledge exchange.
- By partnering with global leaders in welding technology, Nigerian welders can gain access to state-of-the-art equipment, training programs, and best practices.
- These collaborations can help improve the quality and efficiency of welding projects in Nigeria, making local welders more competitive on the global stage.
- Through technology transfer initiatives, Nigerian welders can acquire new skills, expand their knowledge base, and stay abreast of emerging trends in the welding industry.
Government initiatives to promote vocational training in welding
- The Nigerian government is actively promoting vocational training in welding through various initiatives and programs.
- By investing in vocational education and skills development, the government aims to empower youth with the practical skills needed to succeed in the welding sector.
- Government-sponsored training programs, such as apprenticeships and technical schools, provide aspiring welders with hands-on experience and industry-relevant training.
- These initiatives not only help address the skills gap in the welding industry but also create pathways for career advancement and economic empowerment.
In a nutshell, the future of welding technology in Nigeria is full of promising opportunities for skilled welders to advance their careers and contribute to the country’s economic growth.
With a growing demand for welders in various industries,
the potential for collaboration with international companies, and government support for vocational training,
the welding technology sector in Nigeria is well-positioned for success.
Read: Electrical Engineering Licensing Process in Nigeria
Recent Innovations and Developments in Welding Technology
In the dynamic landscape of welding technology, recent years have witnessed remarkable advancements that are reshaping the industry, particularly in Nigeria.
These developments are not just about improving efficiency but also about embracing cutting-edge solutions to meet the demands of modern construction and manufacturing.
Introduction of Automated Welding Systems
Automated welding systems have revolutionized the welding industry by enhancing precision and productivity. In Nigeria, these systems are increasingly adopted across various sectors, from automotive to construction.
Robots equipped with sophisticated sensors and actuators perform intricate welds with consistent quality, reducing human error and improving safety.
Automated systems are particularly beneficial in high-volume production environments where speed and accuracy are critical.
Companies in Nigeria are investing in robotic welding cells that integrate seamlessly into existing manufacturing processes.
This integration boosts output while maintaining stringent quality standards, positioning Nigerian industries competitively on a global scale.
Advancements in Materials and Welding Techniques
The evolution of materials used in welding has opened new possibilities for innovation. Advanced alloys and composites require specialized welding techniques to ensure structural integrity and durability.
In Nigeria, research institutions and industry leaders collaborate to develop welding procedures tailored to local conditions and materials, promoting sustainable practices and cost-efficiency.
Technological advancements have also led to the refinement of traditional welding techniques such as TIG (Tungsten Inert Gas) and MIG (Metal Inert Gas).
These techniques are optimized with state-of-the-art equipment and consumables,
enabling welders in Nigeria to achieve higher precision and reliability in their work.
Integration of Robotics and Artificial Intelligence in Welding Processes
The integration of robotics and artificial intelligence (AI) is perhaps the most transformative trend in welding technology. AI algorithms analyze data in real-time, optimizing weld parameters for superior performance.
In Nigeria, AI-driven welding systems are being implemented to adjust settings automatically based on material variations and environmental conditions, ensuring consistent weld quality across diverse applications.
Robotic welding arms equipped with AI can adapt to complex geometries and weld profiles,
surpassing human capabilities in efficiency and repeatability.
This innovation not only accelerates production but also reduces operational costs associated with rework and inspection.
Nigerian industries are embracing this technology to enhance competitiveness and meet stringent international standards.
In review, As Nigeria advances in welding technology, the future holds promising opportunities for growth and innovation.
The adoption of automated systems, advancements in materials, and integration of robotics and AI are pivotal in transforming the sector.
By embracing these developments, Nigerian industries are poised to elevate their capabilities,
drive economic progress, and contribute to global manufacturing excellence.
The journey towards a more technologically advanced welding landscape in Nigeria is underway,
promising a future where precision, efficiency, and sustainability converge for greater industrial success.
Read: Systems Engineering for Nigerian Public Sector Projects
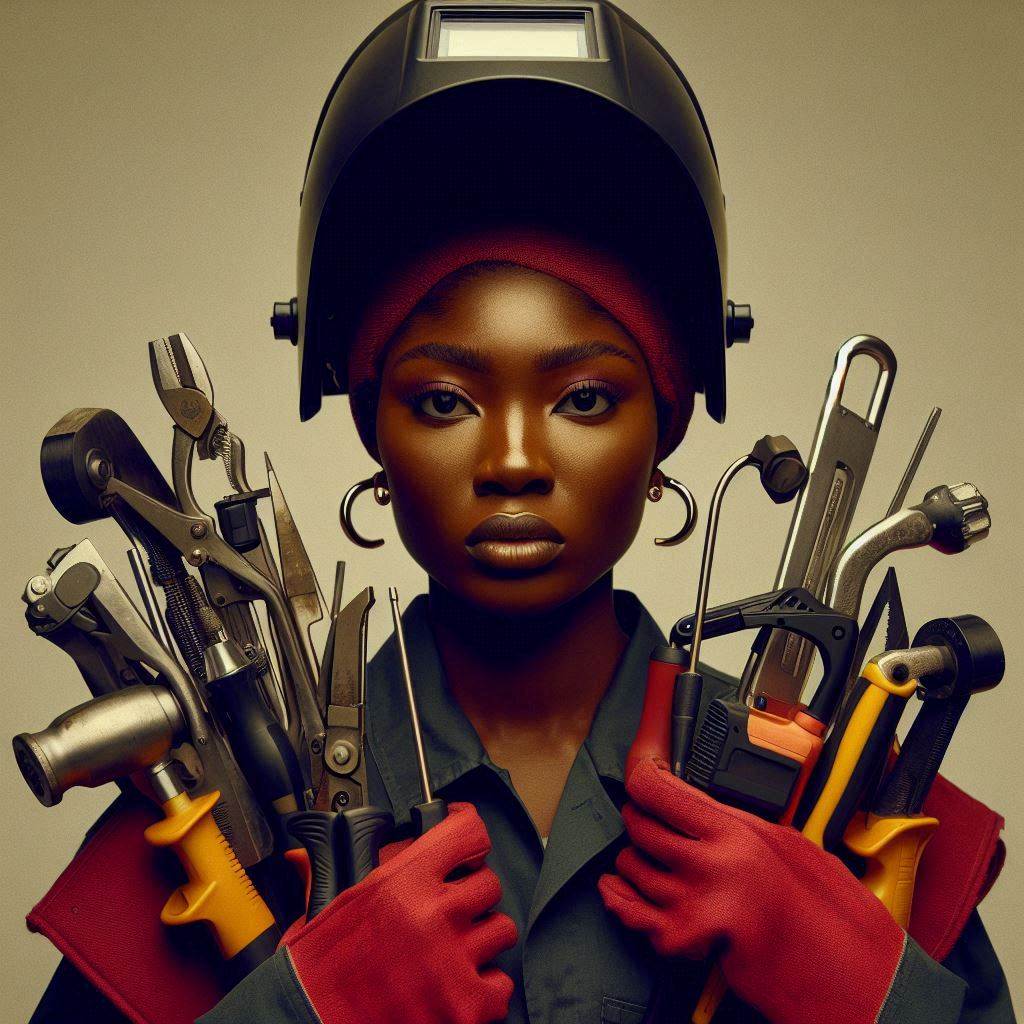
Explore Further: Welding Industry Regulations in Nigeria
Delve into the Subject: Innovations in Quantity Surveying Education
Explore Further: Nigerian Food Engineering: Key Industry Challenges
Future Trends in Welding Technology in Nigeria
Shift towards Eco-friendly and Sustainable Welding Practices
One of the future trends in welding technology in Nigeria is the shift towards eco-friendly and sustainable welding practices.
This involves using techniques and materials that minimize environmental impact and promote sustainability.
With increasing awareness of climate change and the need for sustainable practices,
welding industries in Nigeria are gradually embracing green technologies.
Companies are investing in research and development to find new ways to reduce carbon emissions,
waste generation, and energy consumption in welding processes.
This includes using alternative energy sources like solar power for welding operations and implementing recycling programs for waste materials.
By adopting eco-friendly practices, the welding industry in Nigeria can contribute to environmental conservation and reduce its carbon footprint.
Increased Use of Virtual Reality and Augmented Reality in Welding Training
Another trend shaping the future of welding technology in Nigeria is the increased use of virtual reality (VR) and augmented reality (AR) in welding training.
These technologies offer immersive and interactive learning experiences that simulate real-world welding environments.
By using VR and AR, trainees can practice welding techniques in a safe and controlled virtual space before working on actual projects.
This trend is especially beneficial for novice welders who can learn and improve their skills without the risk of accidents or mistakes.
VR and AR also allow for more personalized training experiences,
where individuals can receive feedback and guidance tailored to their specific needs.
As the demand for skilled welders continues to grow in Nigeria,
integrating VR and AR into training programs can help meet this demand more effectively.
Adoption of Industry 4.0 Technologies in Welding Automation
Industry 4.0 technologies refer to the integration of automation, data exchange, artificial intelligence, and other advanced technologies in manufacturing processes.
In the welding industry, the adoption of Industry 4.0 technologies is revolutionizing welding automation practices in Nigeria.
Companies are leveraging smart robotic systems, IoT sensors, and data analytics to improve efficiency, productivity, and quality in welding operations.
By implementing Industry 4.0 technologies, welding companies in Nigeria can achieve higher levels of precision and consistency in weld quality.
Automated systems can perform complex welding tasks with accuracy and speed, reducing the need for human intervention.
This trend is reshaping the future of welding technology in Nigeria by creating smarter,
more automated, and interconnected welding systems that can adapt to changing production demands.
Read: Role of Systems Engineering in Nigerian Infrastructure
Explore Further: Top Universities for Polymer and Textile Engineering in Nigeria
Transform Your Career with Expert Guidance
Get personalized mentorship consulting that’s tailored to your unique path. Our expert advice is actionable and exclusive.
Get StartedYou Might Also Like: The Role of Ethical Hackers in Nigeria’s Security
You Might Also Like: Graduate Opportunities in Nigerian Food Science
Discover More: Food Science Professional Bodies in Nigeria
You Might Also Like: Accredited Computer Engineering Programs in Nigeria
Strategies for Developing Welding Technology in Nigeria
Enhancing Vocational Training Programs for Welders
One of the key strategies for developing welding technology in Nigeria is to enhance vocational training programs for welders.
This can be achieved by improving the curriculum of welding courses to include the latest techniques and technologies.
Additionally, providing hands-on training in modern welding equipment can help prepare welders for the challenges of the industry.
Encouraging Research and Development in Welding Technology
Another important strategy is to encourage research and development in welding technology.
This can be done by funding research projects in universities and research institutions focused on improving welding processes and developing new technologies.
By fostering a culture of innovation in the welding sector, Nigeria can stay competitive in the global market.
Partnering with Private Sector Companies for Technology Investment
Collaborating with private sector companies for technology investment is crucial for advancing welding technology in Nigeria.
By forming partnerships with companies that specialize in welding equipment and materials, Nigeria can gain access to the latest technologies and innovations in the field.
This can lead to the adoption of more efficient and cost-effective welding techniques, ultimately boosting the competitiveness of Nigerian welders in the global market.
In fact, developing welding technology in Nigeria requires a multi-faceted approach that involves enhancing vocational training programs, encouraging research and development, and partnering with private sector companies for technology investment.
By implementing these strategies, Nigeria can build a strong foundation for the future of welding technology in the country.
Learn More: How to Start a Welding Business in Nigeria
Discover More: Freelance vs. In-house Quantity Surveying Careers
Delve into the Subject: Electrical Engineering Project Ideas for Students
Learn More: Aerospace Engineering Equipment Suppliers Nigeria
Conclusion
As we look towards the future of welding technology in Nigeria, there is immense potential for growth and advancement.
Potential for Growth and Advancement
The welding industry in Nigeria is evolving rapidly, with innovations such as robotic welding, advanced materials, and digitalization.
This growth opens up opportunities for increased efficiency, quality, and competitiveness in the manufacturing sector.
Skilled welders will be in high demand to operate these sophisticated technologies and meet the needs of various industries.
Call to Action for Stakeholders
It is crucial for stakeholders in Nigeria to invest in the future of welding technology by providing training and resources.
Government agencies, educational institutions, and industry leaders must collaborate to support the growth of the welding sector.
By investing in infrastructure and skills development, Nigeria can position itself as a hub for welding technology in Africa.
Importance of Staying Updated with Global Trends
Staying updated with global trends in welding technology is essential for Nigerian welders to remain competitive.
Adopting new techniques, materials, and equipment will enhance the quality of work and productivity in the industry.
Continuous learning and adaptation to new technologies will ensure that Nigerian welders can meet international standards and excel in the global market.
In closing, the future of welding technology in Nigeria is bright, with opportunities for growth, investment, and innovation.
Stakeholders must work together to support the advancement of the welding industry and stay ahead of global trends for a competitive edge.